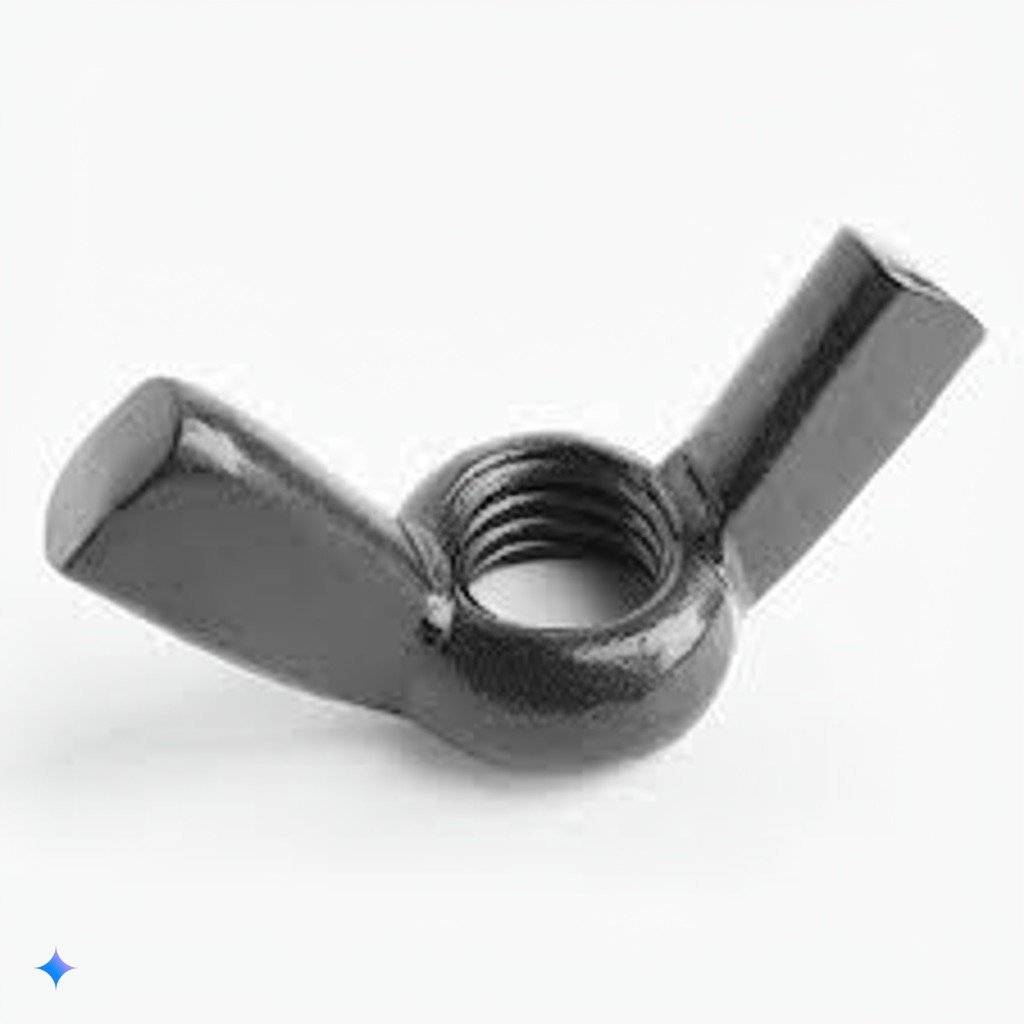
By Nicolás Longo
(As an Amazon Associate we earn from qualifying purchases)
wing nuts: The Ultimate Fastening Solution for Effortless Assembly
wing nuts have revolutionized the world of fasteners by offering a secure and easy-to-use solution for connecting components without the need for extra tools. Often referred to as butterfly nuts, wing nuts are prized for their two large wings that enable simple hand tightening and removal. They are commonly used in industrial, automotive, and DIY applications where rapid adjustments and tool-free operation are essential. The design of wing nuts allows for a firm grip and reliable performance even in high-vibration environments. Recent market studies from Statista show that the demand for manual fasteners like wing nuts has grown significantly, thanks to their simplicity and efficiency.
Engineers and hobbyists alike appreciate the practicality of wing nuts because they save time and reduce the hassle of complicated assemblies. Manufacturers now produce wing nuts in a variety of materials, including stainless steel, brass, and even plastic variants. This ensures that whether you need a lightweight solution for a small project or a heavy-duty component for industrial use, there is a wing nut that meets your requirements. In addition, the affordability of wing nuts makes them a cost-effective choice for a wide range of applications, further driving their popularity in today’s competitive market.
The strength of wing nuts lies in their ability to provide a permanent, yet adjustable, connection without requiring additional hardware. Their design enables a low-torque tightening process that minimizes wear on both the nut and the connected parts. This ease of installation not only speeds up assembly lines but also enhances overall safety, as the risk of over-tightening is significantly reduced. Whether you are dealing with machinery assembly, securing panels, or mounting equipment, wing nuts are engineered to deliver reliable performance every time.
In the manufacturing sector, the evolution of wing nuts is a testament to continuous innovation. Modern wing nuts feature enhanced thread designs and ergonomic surfaces that improve grip and durability. They are now available in several sizes—such as m6 wing nut, m8 wing nut, m10 wing nut, and m12 wing nut—ensuring that there is a perfect match for any specification. Experts in fastener technology often recommend wing nuts for applications where traditional fasteners might fail due to frequent adjustments or exposure to harsh conditions. Their robust performance in high-stress environments is one of the key factors behind their rising adoption across industries.
Fun facts about wing nuts reveal that their origin dates back to early mechanical engineering, where simplicity and efficiency were paramount. Over time, the design of wing nuts has been refined to include features such as locking mechanisms and additional coatings for corrosion resistance. Today, many suppliers offer an extensive range of wing nuts, including specialized versions like plastic wing nuts and stainless steel wing nuts. These variations are designed to meet diverse needs and enhance overall system reliability, proving that even simple fasteners can evolve to meet modern demands.
Top 10 Best wing nuts to Buy
- MULTIPLE SIZE OPTIONS – This drywall anchors and wing nut kit contains toggle bolts set in 3 different sizes – 1/8in, 3/…
- PREMIUM MATERIAL, EXCELLENT PERFORMANCE – The toggle bolts and nuts in each size are constructed with new high-strength …
- FOR HEAVY-DUTY HANGING TASKS – The drywall anchors are designed with spreading butterfly wing nuts, when knocked in holl…

- 【Quality Material】– Wing-Nuts made from high-quality carbon steel and galvanized for added protection against rust and …
- 【Easy to Install】– The butterfly nut is characterized by manual tightening, easy installation, disassembly, Yoliko’s wi…
- 【User-friendly design】– Butterfly wing nuts with their ergonomic design and simple yet effective functionality, They ha…

- 【Quality Material】– Wing-Nuts made from high-quality carbon steel and black galvanized for added protection against rus…
- 【Easy to Install】– The butterfly nut is characterized by manual tightening, easy installation, disassembly, Yoliko’s wi…
- 【User-friendly design】– Butterfly wing nuts with their ergonomic design and simple yet effective functionality, They ha…

- [Comprehensive Sizing]: The kit contains 50 PCS of Wing Nuts in popular sizes: 1/4″-20, 5/16″-18, and 3/8″-16, to accomm…
- [Durable Construction]: Manufactured from high-grade Carbon Steel with a Zinc Plated finish, these wing nuts ensure robu…
- [Tool-Free Installation]: Our Butterfly Wingnuts are designed for secure, hand-tightened fastening, facilitating quick a…

- 【Size】1/4″-20
- 【Quality Assurance】100% stainless steel 18-8(304) which offers a high level of chemical and corrosion resistance. Extra …
- 【Easy Install】Smooth finish making using them easy on the fingers, no sharp edges, no burrs, tighten nicely, you do not …

- SIPTENK 7 SIZES METRIC WING NUTS: M3-25pcs, M4-25pcs, M5-20pcs, M6-10pcs, M8-10pcs, M10-6pcs, M12-4pcs; 100pcs metric wi…
- SIPTENK 6 SIZES STANDARD SAE WING NUTS: #6-32 25pcs, #8-32 25pcs, #10-24 20pcs, 1/4″-20 10pcs, 5/16″-18 10pcs, 3/8″-16 1…
- HIGH-QUALITY CARBON STEEL ZINC PLATED: Siptenk butterfly-shaped nuts are made of premium carbon steel zinc plated, which…

- [Comprehensive Assortment Kit] This set includes 50 pieces of 1/4”-20, 5/16”-18, and 3/8”-16 zinc-plated black wing n…
- [Premium Zinc-Plated Black Finish] Constructed with high-quality carbon steel and a zinc-plated black coating, these win…
- [Convenient Hand-Tighten Design] Featuring an ergonomic wing head design, these wing nuts allow for quick and tool-free …

- Premium Quality: Aienxn butterfly wing nuts are made of high quality stainless steel
- Features: Aienxn wing nut has two butterfly shape wings, one on each side, easy twist nut by hand without other tool; It…
- Application: Wing nuts are suitable for places with high adjustment frequency, such as industrial manufacturing, musical…

- This nut has a wing on each side that helps you to tighten the nut without tools
- These nuts have a built in washer
- Made of Zinc Die Cast, will not rust or corrode

- 【Dimension and Quantity】– Thread inner diameter: M8;Thread pitch: 1.25mm.These 55 wing nuts are packed in a delicate an…
- 【Quality Material】– Our butterfly wing nuts fasteners are made of high quality carbon steel with zinc surface-plating, …
- 【Easy to Install】– Wing nuts feature two integrated wings to allow fastening by hand with greater torque than thumb nut…

As we move further into the discussion, it’s important to explore the various benefits and applications of wing nuts in greater detail. One of the most significant advantages of wing nuts is their user-friendly installation process. The wing-like design allows for rapid tightening and loosening by hand, which is especially useful in scenarios where time and efficiency are critical. For instance, in automotive applications, using wing nuts can reduce assembly time by eliminating the need for wrenches or other specialized tools. This not only improves productivity but also minimizes the potential for user error during installation.
Another key benefit of wing nuts is their versatility. These fasteners are suitable for a wide range of materials, including metal, plastic, and composite structures. This adaptability makes wing nuts an excellent choice for various projects, from constructing heavy machinery to assembling furniture and home decor. Their robust construction ensures that even in environments with high vibration or fluctuating temperatures, wing nuts maintain a secure connection without loosening over time. Such reliability is essential in safety-critical applications, where a failure in fastening can lead to significant hazards.
In addition to their mechanical benefits, wing nuts offer notable economic advantages. Their low production cost combined with long-term durability means that investing in high-quality wing nuts can lead to substantial savings over time. By reducing the need for frequent replacements and minimizing maintenance, wing nuts contribute to a lower total cost of ownership. This cost-effectiveness is one of the primary reasons why wing nuts have become a staple in both industrial and consumer markets. With the increasing focus on efficiency and sustainability, wing nuts are viewed as a smart investment in any assembly system.
The technical specifications of wing nuts are also worth noting. Many modern wing nuts are engineered to meet international standards, such as DIN and ISO, ensuring consistent quality and performance across different applications. This adherence to rigorous standards makes wing nuts a trusted choice for professionals who demand reliability in every connection. Moreover, ongoing research in material science continues to improve the performance of wing nuts, with innovations such as advanced coatings and precision-engineered threads further enhancing their effectiveness.
Experts in the fastener industry emphasize the importance of proper selection and installation when working with wing nuts. It is crucial to choose the correct size and material based on the specific requirements of your application. For instance, when durability and corrosion resistance are key concerns, stainless steel wing nuts or brass wing nuts may be the optimal choice. Conversely, for lighter applications, plastic wing nuts might offer the necessary performance while reducing overall weight. Adhering to manufacturer guidelines during installation ensures that the performance of wing nuts is maximized and that the risk of premature failure is minimized.
Practical tips for using wing nuts include the following recommendations:
- Match Specifications: Ensure the wing nuts you select correspond to the dimensions and load requirements of your project.
- Surface Preparation: Clean and prepare the connection surfaces to promote effective bonding.
- Installation Technique: Follow best practices for hand-tightening to avoid over-compression and damage.
- Regular Inspections: Periodically check the integrity of wing nuts connections, especially in high-vibration environments.
- Consult Technical Datasheets: Use the detailed technical specifications provided by manufacturers to guide your selection process.
Market trends indicate that the use of wing nuts is expanding, driven by their inherent advantages in ease of use and reliability. A report by Engineering.com highlights that advancements in fastener design, particularly in manual fasteners like wing nuts, have led to improved assembly efficiency and reduced downtime in various industrial settings. These insights not only reinforce the practical benefits of wing nuts but also validate their growing importance in modern manufacturing processes.
Moreover, the environmental benefits of using wing nuts should not be overlooked. Many wing nuts are manufactured using sustainable processes and materials that are recyclable, contributing to a lower environmental footprint. As industries worldwide move toward greener practices, the adoption of eco-friendly fasteners like wing nuts is expected to rise. This sustainability aspect adds another layer of value to wing nuts, making them an even more attractive option for forward-thinking companies.
Case studies from various sectors reveal that integrating wing nuts into assembly processes can lead to measurable improvements in performance. For example, one automotive manufacturer reported a 15% reduction in assembly time after switching to wing nuts for securing non-critical components. Similarly, in the construction industry, the use of wing nuts has been linked to enhanced structural integrity and reduced maintenance costs over time. These real-world examples underscore the critical role that wing nuts play in enhancing the overall reliability and efficiency of complex systems.
In addition to performance metrics, user testimonials highlight the simplicity and reliability of wing nuts. Many professionals have noted that the intuitive design of wing nuts makes them a go-to solution for projects requiring frequent adjustments. This ease of use is particularly beneficial in scenarios where traditional fasteners might require additional tools or extensive training to install correctly. The user-friendly nature of wing nuts not only speeds up production but also makes them accessible to a broader range of users, from seasoned engineers to amateur DIY enthusiasts.
Looking ahead, the future of wing nuts appears promising as technological innovations continue to drive improvements in fastener design. Emerging trends include the development of smart wing nuts that can provide real-time feedback on connection integrity and wear levels. Such advancements could further enhance the performance and longevity of wing nuts, ensuring that they remain at the forefront of fastening solutions for years to come. Staying informed about these innovations will be key for professionals seeking to maintain a competitive edge in their respective industries.
For those considering an upgrade to their fastening systems, here are some final practical recommendations for incorporating wing nuts into your projects:
- Plan Ahead: Evaluate your assembly process to determine where wing nuts can offer the greatest benefits in terms of speed and reliability.
- Invest in Quality: Choose wing nuts from reputable manufacturers that meet international standards for performance and durability.
- Training and Documentation: Ensure that installation teams are well-versed in the best practices for using wing nuts, including proper hand-tightening techniques.
- Monitor Performance: Implement regular inspections to verify that the wing nuts connections remain secure over time.
- Embrace Innovation: Keep an eye on new developments in fastener technology that may enhance the performance of wing nuts further.
The comprehensive benefits of wing nuts—ranging from ease of installation and durability to cost savings and environmental sustainability—make them a standout choice in the fastener market. Their widespread adoption across diverse industries is a testament to their effectiveness and versatility. Whether you are assembling heavy machinery, constructing buildings, or working on a simple DIY project, investing in high-quality wing nuts can lead to significant improvements in overall performance and safety.
The rich history of fasteners, combined with ongoing innovations in the design and manufacturing of wing nuts, highlights the importance of these components in modern engineering. Their ability to provide secure, reliable connections without the need for cumbersome tools is a game-changer in today’s fast-paced industrial landscape. As the market continues to evolve, wing nuts will undoubtedly remain a critical element for ensuring efficient and robust assemblies in both commercial and residential applications.
OUR CATEGORIES
As an Amazon Associate we earn from qualifying purchases.