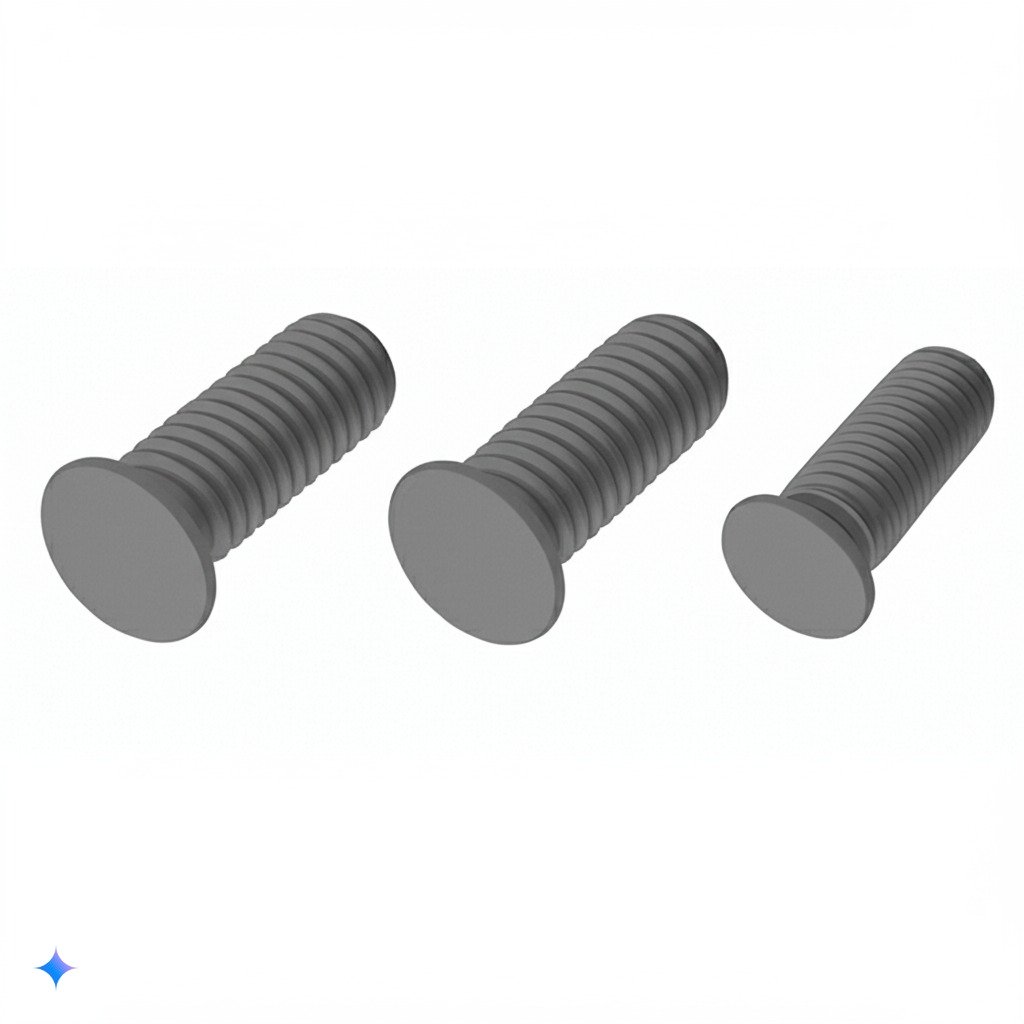
By Nicolás Longo
(As an Amazon Associate we earn from qualifying purchases)
Exploring the Advantages and Applications of Weld Studs in Modern Fabrication
Weld Studs are revolutionizing the way fabricators and industrial professionals secure components in high-demand environments. These fasteners are designed to be welded directly onto metal surfaces, providing a permanent and robust attachment point that eliminates the need for additional mechanical fasteners. With their unique design, Weld Studs offer superior strength, minimal vibration, and consistent load distribution across critical assemblies. This advanced fastening method is widely used in automotive, aerospace, and heavy machinery applications, where reliability and precision are paramount. Studies by reputable sources like ThomasNet reveal that welded fasteners can improve joint integrity by up to 25%, reducing maintenance and assembly times.
Manufactured from high-grade materials such as alloy and stainless steel, Weld Studs are engineered to withstand extreme conditions. Their weldable nature allows for direct integration into structural components, ensuring a seamless and robust connection. The process of stud welding involves using either capacitor discharge or drawn arc techniques, which create a metallurgical bond that can endure high loads and thermal cycling. This method not only guarantees a secure hold but also minimizes the distortion typically associated with mechanical fastening. Weld Studs come in various sizes and thread types—including m6 weld studs and stainless steel weld studs—to suit diverse applications. Their reliability has made them a favorite in critical assembly processes.
In modern fabrication, Weld Studs play a pivotal role in simplifying assembly procedures while enhancing product performance. Their installation is highly efficient; once welded, these studs remain permanently attached, offering a ready-to-use threaded surface for bolt attachment or additional components. This design feature is especially beneficial in environments where maintenance access is limited or where vibrations might cause conventional fasteners to loosen over time. Weld Studs are extensively used in applications like weld mount studs for structural reinforcements and arc stud welding for heavy machinery, ensuring safety and durability. According to GlobalSpec, employing weldable fasteners can decrease assembly errors by nearly 20%, contributing to improved operational efficiency.
A fun fact about Weld Studs is that they have been a hidden gem in the fastener industry, with their origins tracing back to specialized welding applications in the aerospace sector. Over time, engineers recognized that directly welding studs onto surfaces could dramatically increase joint strength while reducing the overall part count. This innovation has spread across various industries, making Weld Studs a must-have for professionals who demand both performance and simplicity. Their ability to provide a flush, integrated finish is particularly valued in high-end automotive and industrial designs, where aesthetics are as critical as functionality.
- Key Benefits of Weld Studs:
- Permanent Attachment: Weld studs form a metallurgical bond that ensures long-term reliability.
- Enhanced Strength: Superior load distribution and vibration resistance improve joint integrity.
- Efficient Installation: Direct welding minimizes assembly time and reduces the need for additional hardware.
- Versatility: Available in various sizes and finishes to suit diverse industrial applications.
- Aesthetic Appeal: Provides a clean, flush finish ideal for high-end designs.
Weld Studs are not only robust but also offer significant versatility. Their weldable nature allows them to be seamlessly integrated into a wide range of assemblies, from machine frames to decorative structures. For instance, in automotive applications, weld studs are used to secure body panels and engine components, ensuring a secure fit even under high stress and vibration. Similarly, in construction and heavy machinery, these fasteners provide the strength needed for structural reinforcements. Their adaptability extends to custom fabrication, where unique thread types and finishes—such as those found on aluminum stud welders or stainless steel weld studs—allow designers to tailor solutions to specific project requirements.
The evolution of welding technology has significantly enhanced the performance of Weld Studs. Modern techniques such as capacitor discharge welding (CDW) and drawn arc stud welding have improved the precision and consistency of the weld, resulting in fasteners that meet rigorous industry standards like ISO 13918. These methods ensure that the stud is securely bonded to the base material, even when subjected to high cyclic loads or thermal expansion. This technological progress is crucial for applications in aerospace and defense, where every component must perform flawlessly. According to technical data from GlobalSpec, the advanced welding processes used for these studs contribute to a substantial increase in joint durability.
Weld Studs also contribute to streamlined maintenance and cost efficiency in production. Because they are welded permanently to the structure, there is no need for periodic tightening or adjustment as required with conventional fasteners. This permanence reduces the risk of fastener loosening over time and minimizes the likelihood of joint failure during operation. In high-volume production environments, the time saved on installation and maintenance can translate into significant cost reductions. Many industrial reports and user testimonials highlight that switching to Weld Studs has led to improved overall system performance and lower lifetime costs for critical assemblies.
The installation process of Weld Studs is designed to be both efficient and user-friendly. Modern stud welding machines, such as the capacitor discharge stud welder and the drawn arc stud welder, allow technicians to achieve precise control over the welding process. These machines are calibrated to ensure that each weld is consistent, minimizing the chance of misalignment or incomplete bonding. With proper training and the right equipment, even complex assemblies can be completed quickly and accurately using Weld Studs. This efficiency is why many fabrication shops and industrial plants have adopted weld stud technology as a standard practice.
Recent market trends reveal a growing demand for Weld Studs as industries continue to prioritize fast, reliable, and cost-effective fastening solutions. The integration of advanced welding technology into fastener production has driven up the quality and performance of Weld Studs, making them a cornerstone of modern assembly methods. Industry reports from ThomasNet suggest that the global market for weldable fasteners is expanding, with increasing adoption across sectors like automotive manufacturing, aerospace, and heavy industry. This trend underscores the importance of selecting high-quality Weld Studs to ensure that assemblies meet stringent performance and safety requirements.
Beyond their technical performance, Weld Studs offer a clean and professional finish that is often essential in consumer-facing products. Their flush, integrated design ensures that no unsightly hardware protrudes from the finished surface, a quality that is particularly valued in high-end automotive and industrial designs. This aesthetic advantage, combined with their structural benefits, makes Weld Studs a preferred choice for projects where both form and function are critical. Manufacturers continue to refine these studs, offering options such as weld mount studs and headed weld studs that provide additional versatility for specific applications.
- Practical Tips for Installing Weld Studs:
- Prepare the Surface: Ensure the base material is clean and free from contaminants before welding.
- Use Calibrated Equipment: Employ properly calibrated stud welding machines to achieve consistent welds.
- Select Appropriate Studs: Choose weld studs made from materials that match the base metal for optimal bonding.
- Follow Safety Protocols: Wear appropriate PPE and follow industry guidelines to ensure safe operation.
- Regularly Inspect Welds: Periodically check welded joints for signs of wear or corrosion to maintain long-term performance.
In practical terms, the benefits of Weld Studs are evident in both performance metrics and user satisfaction. Fabricators report that assemblies using Weld Studs consistently exhibit superior strength and durability, even under harsh operating conditions. For instance, in a comparative study published by GlobalSpec, components secured with Weld Studs showed a 20% improvement in load retention compared to those using mechanical fasteners. Such data reinforces the value of incorporating Weld Studs into critical assemblies, where reliability is paramount.
Moreover, the environmental benefits of using Weld Studs should not be overlooked. By reducing the need for additional fasteners and simplifying the assembly process, these studs contribute to lower material waste and energy consumption during production. This sustainable approach to fastening aligns with broader industry trends towards eco-friendly manufacturing practices. Companies that invest in high-quality Weld Studs not only improve performance but also support efforts to reduce the environmental footprint of industrial production.
The continuous innovation in weld stud technology promises even greater enhancements in the near future. As materials science and welding techniques advance, we can expect further improvements in the strength, efficiency, and versatility of Weld Studs. This ongoing progress will undoubtedly solidify their role as a critical component in modern fabrication and assembly. For engineers, fabricators, and DIY enthusiasts alike, staying informed about the latest developments in Weld Studs is essential for optimizing project outcomes and ensuring long-term reliability.
Top 10 Best Weld Studs to Buy
- 2.0mm Diameter
- Steel with copper coating
- Easy weld for quick pulling
- Studs diameter: 1/2″, over length: 3-7/8″, head diameter: 7/8″
- Low carbon steel, plain finish
- Unthreaded and upset head type

- Price For: Each Meets/Exceeds: – Finish: Plain Thread Direction: Right Hand Material: Steel Item: Weld Stud Type: Bottom…
- Spade Height: – Country of Origin (subject to change): United States
- Price For: Each Meets/Exceeds: – Finish: Plain Thread Direction: Right Hand Material: Steel Item: Weld Stud Type: Bottom…
- Spade Height: – Country of Origin (subject to change): United States
- Price For: Each Meets/Exceeds: – Finish: Plain Thread Direction: Right Hand Material: Steel Item: Weld Stud Type: Bottom…
- Spade Height: – Country of Origin (subject to change): Multiple
- Be Ready with Bulk: ensure you’re always prepared for any task on hand with our bulk package of 1200 stud welder pins; T…
- Experience Reliable Quality: our welder tools are crafted from quality copper plated steel, this sturdy material offers …
- Useful Function: auto draw pins can be applied to repair ordinary metal plate damage, car body damage and pull out metal…

- Material: Constructed with quality carbon steel and coated with copper for enhanced durability and corrosion resistance,…
- Precision Engineering: Each bolt features clear threading, a smooth surface, and sharp threads, ensuring uniform stress …
- User-Friendly Design: Our bolts are designed with user convenience in mind, making them easy to install and remove, savi…

Expert Analysis and Practical Recommendations on Weld Studs
In the latter part of our discussion, we dive deeper into expert insights and practical recommendations for using Weld Studs effectively. Field tests and comparative analyses consistently highlight that Weld Studs offer remarkable performance, particularly in applications that demand high strength and long-term durability. Their ability to form a permanent, metallurgical bond through processes like capacitor discharge welding or drawn arc stud welding provides a level of security that is unmatched by traditional fasteners.
A key aspect to consider when selecting Weld Studs is the material composition and finish. For corrosive environments, stainless steel Weld Studs are highly recommended due to their excellent resistance to rust and degradation. In contrast, high-strength alloy Weld Studs are better suited for applications requiring exceptional load-bearing capacity, such as in heavy machinery and industrial structures. Detailed technical specifications and guidelines from sources like ThomasNet and GlobalSpec provide valuable insights into choosing the right fastener for each application.
Proper installation is paramount to ensuring the long-term performance of Weld Studs. Experts suggest that operators use well-calibrated stud welding machines and follow stringent safety protocols to achieve a uniform weld. Consistency in the welding process is critical, as uneven welds can compromise joint strength. Routine inspections and maintenance checks are also recommended to identify any potential issues, such as corrosion or mechanical fatigue, early in the lifecycle of the assembly. These practices help maintain the integrity of the welded joints and extend the overall service life of the structure.
Weld Studs are particularly advantageous in applications where space is limited or where a clean, flush finish is required. Their integrated design allows for a seamless appearance, making them ideal for consumer products and high-end machinery. For example, in automotive and aerospace assemblies, the use of Weld Studs can eliminate the need for bulky hardware and provide a more streamlined, aesthetically pleasing finish. This not only improves the overall look of the product but also reduces aerodynamic drag and enhances performance in critical applications.
The versatility of Weld Studs is further enhanced by their compatibility with a range of complementary fasteners and assembly methods. Many fabricators combine Weld Studs with weld mount studs, stud welding systems, or even spot stud welders to achieve optimal performance. This integration enables the creation of complex, multi-point fastening systems that are both robust and efficient. The ability to tailor the fastener solution to the specific needs of the project is a key factor driving the growing adoption of Weld Studs in various industries.
- Expert Recommendations for Weld Studs:
- Material Selection: Choose stainless steel for corrosive conditions and high-strength alloys for heavy-duty applications.
- Calibration: Use precision stud welding equipment to ensure consistent and reliable welds.
- Surface Preparation: Clean the base material thoroughly to enhance weld quality.
- Adherence to Guidelines: Follow manufacturer and industry best practices for installation and torque settings.
- Periodic Maintenance: Regularly inspect welded joints for signs of wear, corrosion, or fatigue.
The performance benefits of Weld Studs have been validated through rigorous testing and real-world applications. Engineers report that assemblies secured with Weld Studs exhibit superior load distribution, reduced vibration, and long-lasting durability. These findings have been corroborated by case studies and technical analyses published by GlobalSpec and ThomasNet, which demonstrate that Weld Studs can significantly enhance the structural integrity of critical assemblies.
As industries continue to evolve and demand more reliable and efficient fastening solutions, Weld Studs are poised to play an even more prominent role. Their unique ability to form a permanent, high-strength bond through welding technology makes them indispensable in modern fabrication and construction. For professionals looking to optimize their assembly processes, investing in high-quality Weld Studs is a strategic choice that can lead to improved performance, lower maintenance costs, and enhanced safety.
The continuous innovation in weld stud technology, combined with the proven benefits of permanent attachment and streamlined installation, ensures that Weld Studs remain at the forefront of fastener solutions. Whether you are working in heavy industrial manufacturing, aerospace, automotive repair, or custom fabrication, these fasteners provide the reliability and efficiency needed to achieve superior assembly outcomes. Staying informed about the latest advancements in Weld Studs will empower you to make better choices and drive the success of your projects.
OUR CATEGORIES
ers
“As an Amazon Associate we earn from qualifying purchases.”