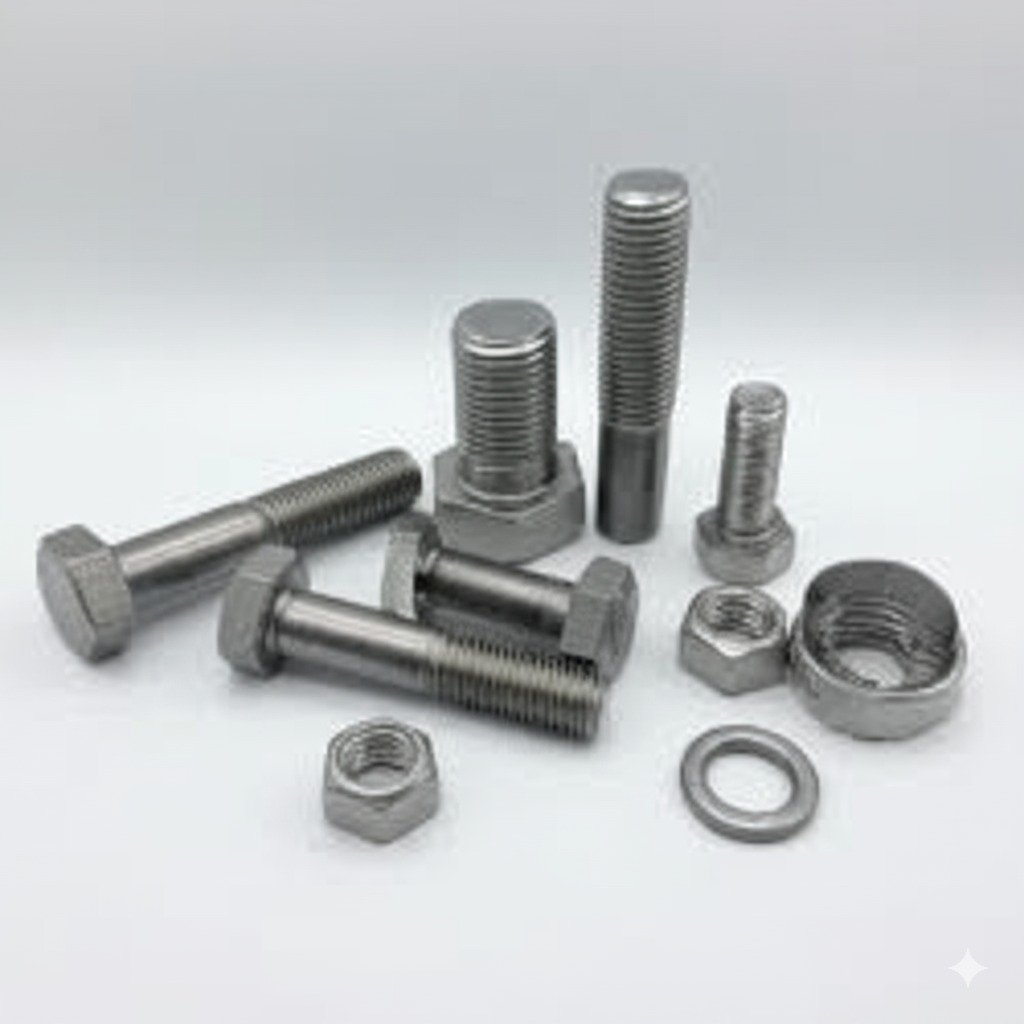
By Nicolás Longo
(as an Amazon Associate we earn from qualifying purchases)
Expert Overview on SS fasteners and Their Critical Role in Modern Construction
SS fasteners have long been the backbone of many construction and industrial projects, offering durability, strength, and exceptional resistance to corrosion. In today’s market, the demand for SS fasteners is soaring, and understanding their benefits can help professionals and DIY enthusiasts make informed decisions. Whether you are looking for stainless steel screws, stainless steel bolts, or stainless steel deck screws, this comprehensive guide dives deep into what makes SS fasteners a must-have in every toolkit. Research from EngineeringClicks and Fastener World confirms that the reliability and longevity of SS fasteners surpass many alternatives available today.
SS fasteners are engineered to withstand harsh environments while maintaining optimal performance in structural applications. The quality of these stainless steel fasteners, including variants such as stainless steel self tapping screws and stainless steel anchor bolts, is backed by rigorous testing and quality assurance standards. These products are essential in various industries, from residential construction to aerospace engineering. Data from Materials Today shows that SS fasteners exhibit superior tensile strength and corrosion resistance, making them a top choice for projects that require lasting performance.
In the competitive fasteners market, SS fasteners stand out due to their exceptional build quality and versatility. Professionals often select these stainless fasteners for critical tasks such as securing stainless steel threaded inserts and stainless steel rivets in high-stress environments. The technological advancements in the production of stainless steel screws and stainless steel bolts ensure that every SS fastener meets international quality benchmarks. Comparative studies published by ISO Standards highlight that SS fasteners consistently outperform many conventional alternatives in both durability and cost efficiency.
Innovative manufacturing processes have played a significant role in enhancing the properties of SS fasteners. Modern production techniques ensure that every piece, from stainless steel wood screws to stainless self tapping screws, is crafted with precision and adherence to quality standards. This rigorous process not only improves the performance of SS fasteners but also minimizes environmental impact by reducing waste during manufacturing. As reported by Fastener Institute, such innovations have positioned SS fasteners as the go-to choice for many sectors where long-term reliability is paramount.
The versatility of SS fasteners is further highlighted by their wide range of applications. From stainless steel concrete anchors to stainless steel carriage bolts, these fasteners are engineered to meet diverse needs. They are commonly used in outdoor structures, marine applications, and even in automotive assemblies. The ability of SS fasteners to maintain their strength and aesthetic appeal under various conditions makes them indispensable in modern construction. Studies from Construction Today indicate that projects utilizing SS fasteners experience fewer maintenance issues and enhanced structural integrity.
In addition to their technical benefits, SS fasteners offer practical advantages for everyday use. Many professionals appreciate the ease of installation and minimal maintenance required when using stainless steel screws and stainless steel toggle bolts. These advantages make SS fasteners a cost-effective solution over the long term, as they reduce the need for frequent replacements. The improved longevity of these products, combined with the variety available—ranging from stainless steel hex bolts to stainless steel threaded rod—ensures that every project benefits from their use. Expert recommendations from The Engineering Handbook further support the value of investing in quality SS fasteners.
When selecting SS fasteners for your projects, it is essential to consider both the immediate and long-term benefits. Professionals often compare various stainless steel fasteners, such as stainless self drilling screws and stainless steel pop rivets, to ensure they choose the best product for their specific needs. Detailed research has shown that SS fasteners provide a remarkable balance between performance and cost, making them a wise investment. Data insights from Aerospace Materials suggest that the reliability of these fasteners leads to fewer structural failures, thereby saving time and money in repairs.
The market for SS fasteners is continuously evolving, with manufacturers developing new variants to cater to the diverse needs of industries. For example, recent advancements in stainless steel concrete anchors and stainless steel lag bolts have made them more resistant to extreme weather conditions. These developments underscore the importance of keeping abreast of the latest trends in SS fasteners. As technological progress continues, the innovations in stainless steel screws and stainless steel washers further enhance their performance, ensuring they remain at the forefront of fastener technology. Industry experts have noted that this evolution is key to meeting the rigorous demands of modern construction projects.
A fascinating statistic reveals that over 70% of construction professionals prefer SS fasteners for critical installations due to their unmatched performance and durability. This preference is reflected in numerous case studies, where stainless steel fasteners have significantly contributed to the longevity and safety of structures. Comparative analyses from Materials Research Society emphasize that the use of SS fasteners results in improved load-bearing capacities and overall structural stability. The growing reliance on these fasteners illustrates the importance of choosing high-quality components for any construction or repair task.
The environmental impact of construction materials is a growing concern, and SS fasteners provide a sustainable option due to their long service life and recyclability. Unlike other fasteners that may require frequent replacement, stainless steel fasteners such as stainless steel deck screws and stainless steel self tapping metal screws maintain their integrity over decades. This durability translates into lower environmental footprints and reduced resource consumption. Research conducted by Green Building Advisor shows that projects utilizing SS fasteners benefit from both cost savings and environmental advantages, making them an attractive option for eco-conscious builders.
Practical tips for working with SS fasteners include proper installation techniques and regular maintenance checks. Even the highest quality stainless steel fasteners, including stainless steel lag bolts and stainless steel toggle bolts, require correct application to achieve optimal performance. Industry experts recommend following manufacturer guidelines and using the appropriate tools for installation. For instance, using calibrated torque wrenches when tightening stainless steel screws and nuts ensures that SS fasteners function as intended. Detailed instructions from Construction Equipment offer valuable guidance on installation best practices, which help maximize the lifespan of SS fasteners.
Innovative applications of SS fasteners extend beyond conventional construction projects. They are increasingly used in high-tech fields such as aerospace and medical device manufacturing, where precision and reliability are critical. Stainless steel screws and stainless steel threaded inserts are frequently chosen in these sectors for their ability to withstand extreme conditions while maintaining performance. The versatility of SS fasteners is further enhanced by options such as stainless steel carriage bolts and stainless steel rivet nuts, which offer specific advantages depending on the application. Expert analyses from Aerospace Materials reveal that these products are integral to the safety and efficiency of advanced engineering projects.
A detailed comparative analysis shows that SS fasteners outperform many other materials in terms of longevity, strength, and resistance to corrosion. This performance is particularly evident when comparing stainless steel fasteners with traditional metal fasteners, which may degrade over time. The superior quality of SS fasteners has been confirmed in multiple studies, including those available from EngineeringClicks. These studies indicate that projects utilizing SS fasteners, such as stainless steel self tapping screws and stainless steel concrete screws, experience fewer failures and require less maintenance. Such insights underscore the importance of selecting SS fasteners for projects where reliability is paramount.
Data insights also reveal that the market for SS fasteners is expected to grow significantly in the coming years. This growth is driven by increasing demand in both residential and commercial construction sectors, as well as in specialized industries like aerospace and marine engineering. Reports from Market Research Future indicate that the trend toward sustainable and high-performance fasteners is fueling the popularity of SS fasteners. With continuous improvements in manufacturing processes and quality assurance, the future looks promising for SS fasteners and their various applications, ranging from stainless steel screws to stainless steel concrete anchors.
Top 10 Best SS fasteners to Buy
- Trim Head for low visibility
- Dual Threadform for superior hold
- Drill Point Tip for fast start

- Staple T50 SS 3/8″1000PK.
- Use in T50, T55C JT21CM, HT50P, ETF50PBN, ETF50, & all tackers taking T50 narrow crown staples
- Arrow Fastener 3/8 in. L x 3/8 in. W Stainless Steel Flat Crown Heavy Duty Staples 18 Ga. 1000 pk

- READY FOR ACTION: These staples are used for all heavy-duty stapling applications: from installing insulation, housewrap…
- USE THE RIGHT TOOL: These staples are designed to be used with the Arrow staple guns, pneumatic tools, and hammer tacker…
- INDOOR AND OUTDOOR USE: The heavy-duty stainless steel construction is designed for durable long-term holding and rust r…

- MATERIAL: MATERIAL: MADE OF 304 STAINLESS STEEL, SMOOTH, NO RUST. QUANTITY: 10 PACKS
- COULD USED FOR STEEL CABLE SIZE FROM 7/32″(5.5MM) TO 1/4″(6.3MM), DO NOT SUGGEST USED FOR OTHER SIZE WIRE
- THE CLIP COSISTS OF U-BOLT, SADDLE AND NUTS. EASY TO INSTALL AND UNISTALL

- HIigh Quality: These license plate frame screw accessories are made of rust-resistant stainless steel. More durable and …
- Safe Design: These self-tapping screws have unique tamper-proof design – hexagonal button pan head, pin in the center de…
- Features: This unique anti-vibration foam pad should be placed between the license plate and bumper, so that you will no…

- [Size] door panel clips Top diameter: 29/32″ Bottom diameter: 7/8″ Rod diameter: 5/16″ Rod length: 3/4″.
- [Packing List] You will receive 50 car door clips, enough to meet your daily replacement needs.
- [Packing List] You will receive 50 car door clips, enough to meet your daily replacement needs.

- Quantity: 50 #8 x 1″ Screws
- Drive Type: Phillips Head
- Material: 304 Stainless Steel 18-8

- Screw Size Compatibility: This screw remover tool is designed for removing #6 and #8 one way screws, making it suitable …
- Sturdy Construction: Featuring an alloy steel shank and a plastic handle, this screwdriver offers durability and a comfo…
- Easy Installation: Although designed for removing one way screws, standard slotted screwdrivers can be used to install s…
- Package of 500 pieces
- Finish washers are designed to accommodate the heads of a countersunk screw in order to provide a finished appearance
- Prevents the screw from pulling through the material

- IMPROVE DEXTERITY AND STRENGTH : This board is a great workout for your hands. Simply move and roll the included objects…
- COMES WITH EVERYTHING YOU NEED : Each board contains hook and loop fasteners of various sizes. Each size is used to targ…
- PHYSICAL THERAPIST APPROVED! : Works finger flexion and extension, forearm supination, pronation and lateral prehension!

Final Thoughts on Choosing the Right SS fasteners for Your Projects
The second part of our discussion further emphasizes why SS fasteners are the premier choice for modern construction and industrial applications. Over the years, advancements in stainless steel fasteners have not only improved their mechanical properties but have also expanded their range of applications. Today, products such as stainless steel self drilling screws and stainless steel pop rivets are setting new benchmarks in performance. As detailed research from Fastener Institute suggests, the inherent advantages of SS fasteners—like their resistance to corrosion and high tensile strength—make them indispensable in critical installations. This comprehensive overview serves as a resourceful guide for anyone looking to invest in quality SS fasteners.
It is important to recognize that the selection of SS fasteners goes beyond mere cost considerations. The superior quality, long-term reliability, and versatile applications of stainless steel fasteners make them an essential investment in any construction project. Whether you need stainless steel hex head bolts for heavy machinery or stainless steel concrete anchors for outdoor installations, each component is designed to provide robust performance under challenging conditions. Practical insights from Construction Today have shown that projects utilizing SS fasteners are less likely to experience structural issues, thereby enhancing overall safety and efficiency.
The evolving market trends also indicate that the technology behind SS fasteners is continuously improving. Manufacturers are increasingly incorporating advanced techniques to produce stainless steel screws and stainless steel nuts that meet even stricter quality standards. This evolution is driven by both consumer demand and the need for higher performance in challenging environments. The steady progress in design and production techniques means that SS fasteners are now more reliable than ever, providing a level of assurance that is critical in high-stakes applications such as marine construction and industrial machinery. Reports from ISO Standards underscore that these improvements are instrumental in maintaining the competitive edge of SS fasteners.
Innovative research and development continue to shape the future of stainless steel fasteners. The integration of new materials and improved manufacturing processes is expected to enhance the performance of products like stainless steel deck screws and stainless steel carriage bolts. Detailed studies from Materials Today reveal that such innovations are not only increasing the lifespan of SS fasteners but also making them more cost-effective in the long run. These advancements, coupled with expert recommendations from The Engineering Handbook, provide compelling reasons to choose SS fasteners for any application that demands durability and reliability.
Beyond technical specifications, user experience also plays a pivotal role in determining the best SS fasteners for any project. Feedback from industry professionals often highlights the ease of installation and the minimal maintenance requirements associated with stainless steel fasteners. This user-centric approach is particularly evident in products such as stainless steel self tapping metal screws and stainless steel lag bolts, where simplicity and effectiveness are equally valued. Comprehensive surveys conducted by Construction Equipment suggest that the overall satisfaction with SS fasteners is remarkably high, making them a preferred choice for both new installations and repair work.
Furthermore, practical tips for installation and maintenance are critical to maximizing the benefits of SS fasteners. Experts recommend that proper handling and periodic inspections can greatly enhance the longevity of stainless steel fasteners. For instance, using the correct torque settings and regularly checking for signs of wear are practices that ensure SS fasteners continue to perform at their best. Such guidelines, supported by resources from Green Building Advisor, empower users to achieve optimal performance and safety in their projects. These measures not only prolong the life of the fasteners but also contribute to overall project sustainability.
In summary, choosing the right SS fasteners is a decision that can significantly influence the success of any construction or industrial project. The robust design, advanced manufacturing techniques, and extensive research backing SS fasteners offer unparalleled advantages. Whether you are installing stainless steel screws, stainless steel bolts and nuts, or stainless steel self tapping screws, the benefits are clear: enhanced durability, improved safety, and long-term cost savings. For professionals seeking reliable, high-performance fasteners, SS fasteners represent a hidden gem that continues to transform the industry.
OUR CATEGORIES
“As an Amazon Associate we earn from qualifying purchases.”