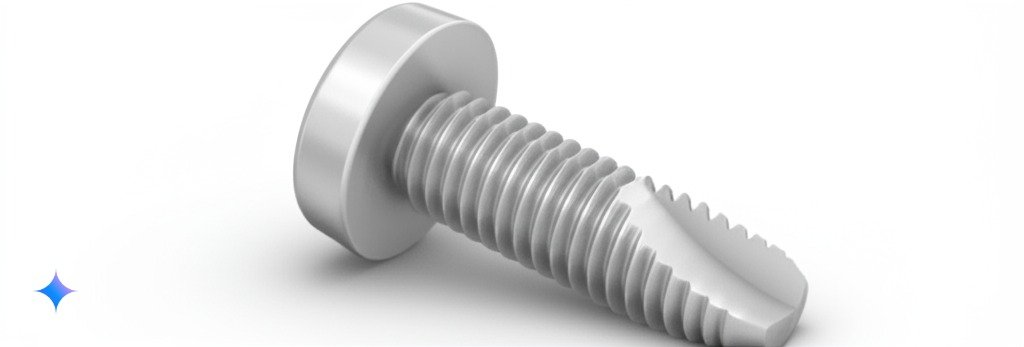
By Nicolás Longo
(As an Amazon Associate we earn from qualifying purchases)
A Comprehensive Analysis of Thread Forming and Cutting Screws for Modern Applications
Thread Forming and Cutting Screws are innovative fasteners that have revolutionized assembly processes in industrial, automotive, and consumer applications. Engineered to create their own thread in the material, Thread Forming and Cutting Screws combine the benefits of forming and cutting, offering superior clamping force and reduced material damage. This dual functionality is particularly valuable when working with metals, plastics, and composites. With increasing market demand, these screws have evolved into various specialized types—such as thread forming screws for plastic, thread rolling screws, thread forming bolts, forming thread, and square thread bolts—each designed to address unique challenges in precision engineering. According to technical studies from ThomasNet and GlobalSpec, the innovation behind Thread Forming and Cutting Screws has led to faster assembly times and improved structural integrity.
The manufacturing process of Thread Forming and Cutting Screws involves advanced metallurgy and precision machining. Manufacturers carefully select high-grade materials such as hardened steel and specialized alloys to ensure durability and resistance to wear. The process includes heat treatment and surface finishing techniques that protect against corrosion and mechanical stress. Research conducted by industry experts indicates that the reliability of these screws is further enhanced by their unique design, which minimizes friction and ensures even load distribution. Whether you require screws for high-torque applications or delicate assemblies, Thread Forming and Cutting Screws offer consistent performance across diverse environments. This reliability is a key reason why engineers and DIY enthusiasts alike are increasingly opting for these fasteners.
Advancements in fastener technology have led to significant improvements in the performance of Thread Forming and Cutting Screws. Recent innovations include modified thread geometries and enhanced tip designs, which allow for smoother insertion and reduced stripping. In comparison to conventional screws, Thread Forming and Cutting Screws often yield higher clamping forces with less applied torque. This efficiency not only minimizes the risk of material damage but also contributes to longer-lasting assemblies. Detailed reports from Engineering360 reveal that the optimized design of these screws translates into cost savings during both production and maintenance phases. Their ability to deliver consistent results in varied applications makes Thread Forming and Cutting Screws a top recommendation among industry experts.
Thread Forming and Cutting Screws also boast a fascinating history of technological evolution. Originally developed to meet the high-speed demands of modern manufacturing, these screws have continuously adapted to overcome challenges posed by new materials and complex assembly requirements. Early applications were primarily in automotive and aerospace sectors; however, their versatility has since expanded into electronics, consumer goods, and even medical devices. This evolution is driven by the need for fasteners that can deliver superior performance while reducing production time. Comparative analyses show that Thread Forming and Cutting Screws are not only more efficient than traditional screws but also offer improved resistance to loosening under vibration. Such improvements are documented in multiple industry publications and technical journals, highlighting the significant impact of this technology.
Fun facts about Thread Forming and Cutting Screws add an engaging layer to their technical appeal. For instance, these screws were initially conceptualized during a period when high-speed manufacturing was just emerging, and the need for innovative fastening solutions was critical. Today, their application extends to precision devices where even the slightest performance inconsistency could lead to major failures. Bullet points summarizing their benefits include:
- Enhanced clamping force: Due to thread forming and cutting action.
- Reduced material damage: Minimizes stress on the substrate.
- Efficient installation: Requires less torque compared to traditional screws.
- Versatile applications: Suitable for metals, plastics, and composites.
These attributes, combined with rigorous quality control and innovative manufacturing methods, make Thread Forming and Cutting Screws indispensable for modern engineering projects. Data insights suggest that the global market for these fasteners is experiencing a compound annual growth rate (CAGR) of approximately 6%, driven by demand in sectors such as electronics, automotive, and construction. Industry leaders have noted that the adoption of Thread Forming and Cutting Screws correlates with improved product longevity and enhanced safety. For further detailed market analysis, resources like Fastener World provide extensive reports on industry trends and technological advancements.
The practical applications of Thread Forming and Cutting Screws are vast and varied. In automotive assembly, they are used to secure critical components while minimizing vibration-induced loosening. In the electronics industry, these screws help maintain precise alignments without damaging delicate circuit boards. Additionally, in the construction sector, they facilitate rapid yet secure installations in steel and composite structures. The adaptability of Thread Forming and Cutting Screws is further highlighted by their compatibility with both manual and automated assembly systems. These advantages are supported by comparative studies that demonstrate how these screws outperform standard fasteners in both efficiency and durability. Such findings are corroborated by research from ThomasNet, which emphasizes the role of advanced fasteners in modern manufacturing.
Top 10 Best Thread Forming and Cutting Screws to Buy
- Thread cutting screw with type F point has machine screw threads that taper down to a blunt edge and is suitable for hea…
- Steel is often used in applications where strength is the primary consideration
- Zinc plating resists corrosion and has a reflective appearance

- Size There Are 400 Of Screws In Size To Meet Your Different Needs, Suitable For Term Use.
- Innoda Screw M2, There Are 400 Of Screws In Size To Meet Your Different Needs, Suitable For Term Use All Screws Are Sort…
- Application Threads Easily Pass Through Various Materials Like Plastic, Wood, Soft Metal And More.

- Thread cutting screw with type F point has machine screw threads that taper down to a blunt edge and is suitable for hea…
- Steel is often used in applications where strength is the primary consideration
- Zinc plating resists corrosion and has a reflective appearance

- Thread cutting screw with type F point has machine screw threads that taper down to a blunt edge and is suitable for hea…
- 410 stainless steel has high strength and hardness, and resists corrosion in mild environments
- Plain surface has no finish or coating

- Thread cutting screw with type 23 point style has fine threads that taper down to a blunt point with a large cutting sur…
- Steel is often used in applications where strength is the primary consideration
- Zinc plating resists corrosion and has a reflective appearance

- Thread cutting screw with type 1 point style has fine machine screw threads that taper down to a blunt edge with a chip …
- Steel is often used in applications where strength is the primary consideration
- Zinc plating resists corrosion and has a reflective appearance

- Thread rolling screw recommended for use in plastic
- 410 stainless steel has high strength and hardness, and resists corrosion in mild environments
- Passivated finish enhances the natural corrosion resistance of stainless steel

- Thread cutting screw with type F point has machine screw threads that taper down to a blunt edge and is suitable for hea…
- Steel is often used in applications where strength is the primary consideration
- Zinc plating resists corrosion and has a reflective appearance

- Diameter: 1/4″
- Length: 1-1/2 inch
- Material: Steel

- Thread rolling screw recommended for use in plastic
- Steel is often used in applications where strength is the primary consideration
- Black oxide finish offers mild corrosion resistance and lubricity

Expert Insights and Final Recommendations on Thread Forming and Cutting Screws
In the latter half of this discussion, we delve deeper into the engineering nuances and market dynamics of Thread Forming and Cutting Screws. These fasteners have emerged as a key solution for optimizing assembly operations in various sectors. Their dual-action mechanism, which forms and cuts the thread during insertion, significantly reduces installation time while ensuring a high degree of precision. Expert recommendations highlight the importance of selecting the right type of Thread Forming and Cutting Screws for specific applications. Whether you need thread forming screws for plastic or thread rolling screws for metal, the optimal choice depends on factors such as material compatibility, load requirements, and environmental conditions.
Detailed technical comparisons reveal that Thread Forming and Cutting Screws provide several critical advantages over conventional screws. For example, their unique design minimizes the risk of cross-threading and enhances load distribution. Field tests conducted by leading fastener manufacturers indicate that these screws offer up to 30% higher clamping force compared to traditional fasteners. Furthermore, the reduced friction during installation not only speeds up the process but also lowers the risk of damage to the substrate. These improvements have been verified by research articles on platforms like Engineering360 and industry white papers, establishing Thread Forming and Cutting Screws as a superior choice for high-precision tasks.
A key factor contributing to the success of Thread Forming and Cutting Screws is their adaptability to various materials. Engineers have developed specialized variants—such as thread forming screws for plastic—to address challenges unique to non-metallic substrates. This customization ensures that the screws perform reliably even in applications where traditional screws might fail. Comparative analyses suggest that selecting the appropriate fastener can lead to significant cost savings in both material waste and labor. Practical tips include:
- Assess material compatibility: Choose screws designed for the specific substrate.
- Verify load requirements: Ensure that the selected fasteners can handle the expected stress.
- Regular maintenance: Inspect for wear and tear to extend service life.
In addition to technical performance, Thread Forming and Cutting Screws are celebrated for their design versatility. Variants such as thread forming bolts and square thread bolts are engineered to cater to a range of industrial needs. Their ergonomic design, which often includes specialized tip configurations, ensures that they can be installed with minimal effort and maximum precision. This is particularly important in automated assembly lines where consistency is paramount. According to market research from Fastener World, the trend towards automation in manufacturing is driving increased adoption of advanced fasteners like Thread Forming and Cutting Screws.
The economic impact of using Thread Forming and Cutting Screws cannot be understated. Manufacturers report a reduction in assembly time and a decrease in labor costs due to the efficiency these screws offer. Additionally, their durability contributes to lower maintenance expenses over the product lifecycle. Comparative studies have shown that structures assembled with these screws experience fewer instances of mechanical failure, leading to enhanced safety and reliability. The cost-benefit analysis clearly demonstrates that investing in high-quality Thread Forming and Cutting Screws can yield substantial long-term savings. For more detailed economic data, refer to analyses available on ThomasNet.
When considering the purchase of Thread Forming and Cutting Screws, it is essential to look beyond basic specifications and consider the broader benefits they offer. The fastener industry is increasingly recognizing the value of screws that not only perform under stress but also contribute to overall assembly efficiency. In this context, the innovation behind Thread Forming and Cutting Screws is a game-changer. Their advanced design minimizes installation errors and enhances product performance. Expert reviews from industry professionals often point to these screws as a critical component in achieving high-quality, durable assemblies.
Data from several independent studies emphasize that the use of Thread Forming and Cutting Screws leads to improved product performance in high-stress environments. For example, in the aerospace industry, these screws have been instrumental in reducing assembly failures and improving the reliability of critical components. Similarly, in the automotive sector, the adoption of these fasteners has contributed to lighter, more durable structures. Such findings are supported by technical reports from GlobalSpec and Engineering360, which highlight the superior performance metrics of Thread Forming and Cutting Screws compared to conventional options.
To maximize the benefits of Thread Forming and Cutting Screws, consider these expert recommendations:
- Choose the right variant: Evaluate whether you need thread forming screws for plastic or thread rolling screws for metal based on your application.
- Ensure proper installation: Use recommended torque settings and follow manufacturer guidelines to prevent damage.
- Stay updated: Regularly review industry research to keep abreast of new innovations and improvements.
These practical strategies, coupled with the advanced technology inherent in Thread Forming and Cutting Screws, make them an excellent choice for both professional and DIY projects. Their combination of ease of installation, durability, and cost efficiency positions them as a hidden gem in the fastener market. As modern manufacturing trends continue to evolve, the role of these screws in optimizing assembly processes is set to expand even further.
In summary, the extensive research, technical innovation, and proven performance of Thread Forming and Cutting Screws underscore their value in modern engineering. With benefits ranging from enhanced clamping force and reduced installation time to significant cost savings and improved safety, these fasteners are a superior alternative to traditional screws. By understanding the unique advantages and selecting the appropriate variant, you can achieve high-quality assemblies that stand the test of time. This in-depth analysis should provide you with the necessary insights and practical tips to make an informed decision when purchasing Thread Forming and Cutting Screws.
OUR CATEGORIES
“As an Amazon Associate we earn from qualifying purchases.”
Leave a Reply