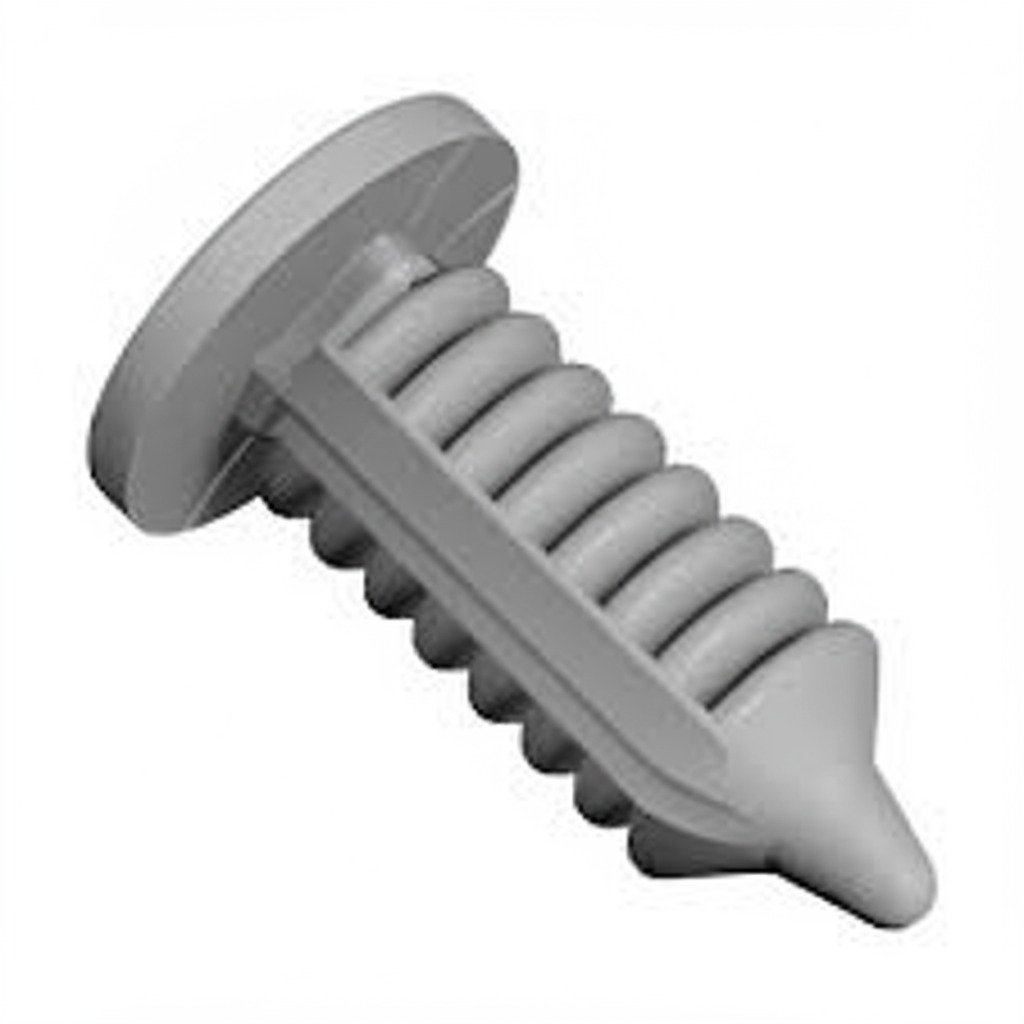
By Nicolás Longo
(As an Amazon Associate we earn from qualifying purchases)
Push-In Rivets are an innovative fastener solution that offer a secure, efficient, and one-sided installation for many applications. In this comprehensive guide, we explore the evolution, technical specifications, and various types of Push-In Rivets available today. Whether you are a seasoned engineer or a DIY enthusiast, understanding Push-In Rivets—from plastic push rivets to metal push rivets and specialized fasteners for automotive and industrial uses—will empower you to make an informed purchase decision. This article combines expert recommendations, fun facts, technical insights, and data-backed research to help you choose the ideal fastener for your project. (Source: Albany County Fasteners)
The Evolution and Importance of Push-In Rivets
Push-In Rivets have transformed the way we secure components in modern assemblies. Originally developed to address the challenges of hard-to-reach installations, Push-In Rivets allow for a one-sided application that is both time-saving and reliable. Their design minimizes installation effort while ensuring a robust mechanical bond, making them popular in industries such as automotive, aerospace, and consumer electronics. The simplicity of using Push-In Rivets has also spurred their adoption in DIY projects and home improvements. Over time, manufacturers have refined these fasteners into specialized forms—ranging from plastic push rivets to metal push rivets—each engineered to meet specific performance standards. (Source: OneMonroe)
Understanding the Mechanism of Push-In Rivets
Push-In Rivets work by inserting the rivet into a pre-drilled hole and applying pressure to force the fastener into place. As the push-in rivet is pressed, its internal components expand, locking the rivet securely against the material. This method eliminates the need for access to the backside of the assembly and simplifies the installation process. The ease of use makes Push-In Rivets an attractive option for rapid assembly tasks in both professional and home settings. Their reliable performance under shear forces and resistance to vibration ensure that connections remain secure over time. (Source: Würth Industry USA)
Material Variants and Their Applications
Push-In Rivets are available in a range of materials, each offering unique benefits.
- Plastic Push Rivets: Lightweight and cost-effective, these are ideal for non-structural applications and projects where corrosion is a concern.
- Metal Push Rivets: Often made from stainless steel or aluminum, metal push rivets provide superior strength and durability in demanding environments.
- Nylon Push Rivets: These offer excellent electrical insulation and are used in electronic assemblies.
The choice of material directly affects the performance, longevity, and suitability of the fastener for specific tasks. For instance, automotive applications may favor metal push rivets for their high strength, while consumer electronics might rely on plastic push rivets for their insulating properties. (Source: Albany County Fasteners)
Technical Specifications and Best Practices
Precision in the installation of Push-In Rivets is crucial for achieving optimal performance. Key specifications include the rivet diameter, grip range, and material thickness compatibility. It is essential to pre-drill holes that match the exact dimensions recommended by the manufacturer. Utilizing calibrated tools such as digital calipers and proper installation equipment, like battery-operated rivet guns, ensures that each Push-In Rivet is installed with the correct pressure and alignment. These best practices prevent common issues like loose sets or pull-through, guaranteeing a secure and lasting bond in your assembly. (Source: Würth Industry USA)
Comparative Analysis: Push-In Rivets vs. Traditional Rivets
Comparing Push-In Rivets to traditional rivets highlights several advantages:
- One-Sided Installation: Unlike conventional rivets, Push-In Rivets allow for installation from a single side, saving time and simplifying the process.
- Enhanced Efficiency: The push-in mechanism reduces the need for complex tools and minimizes the risk of misalignment during installation.
- Versatility: Available in various materials and sizes, Push-In Rivets can be used in a broad spectrum of applications, from automotive repairs to electronic housings.
This comparative analysis demonstrates that Push-In Rivets offer a modern alternative that combines convenience with robust mechanical performance, making them a smart choice for both professionals and hobbyists. (Source: OneMonroe)
Expert Recommendations for Selecting the Right Push-In Rivets
Experts emphasize that the successful application of Push-In Rivets depends on careful selection based on the following factors:
- Material Compatibility: Ensure the fastener material is suitable for the environmental conditions and load requirements of your project.
- Accurate Drilling: Use the correct drill bit size to create holes that perfectly match the rivet dimensions, ensuring a tight fit.
- Tool Quality: Invest in a reliable, high-quality push-in rivet installation tool to achieve consistent results.
- Application Specifics: Consider the unique demands of your project—whether it requires plastic push in fasteners for lightweight assembly or metal push rivets for heavy-duty applications.
Following these guidelines helps guarantee that the chosen Push-In Rivets will deliver maximum performance and durability. (Source: Würth Industry USA)
Installation Best Practices for Push-In Rivets
To ensure the optimal performance of Push-In Rivets, adhere to these installation best practices:
- Surface Preparation: Clean and prepare all surfaces to remove dirt, grease, and debris before installation.
- Precision Drilling: Drill holes that are precisely sized according to the manufacturer’s specifications to prevent misalignment.
- Tool Calibration: Regularly check and maintain your installation tools for consistent pressure and performance.
- Test Installations: Conduct a trial run on scrap material to fine-tune your technique and ensure that the Push-In Rivets secure properly.
- Inspection: After installation, verify that the rivet has expanded fully and that there is no visible slack.
These steps help in achieving reliable, professional-grade results that enhance the structural integrity of your assembly. (Source: Albany County Fasteners)
Market Trends and Consumer Insights on Push-In Rivets
Recent market research indicates a growing preference for Push-In Rivets in industries where efficiency and ease of installation are critical. Trends show that the demand for both plastic and metal push-in fasteners is rising, driven by their versatility in automotive, aerospace, and consumer electronics applications. Consumer reviews highlight the convenience of one-sided installation and the durability of these fasteners under various conditions. Furthermore, statistical data from industrial reports suggests that using Push-In Rivets can reduce assembly time by up to 30% compared to traditional methods, leading to increased productivity and cost savings. (Source: Albany County Fasteners)
Top 10 Best Push-In Rivets to Buy
- UNIVERSAL FIT KIT – Great Assortment Push Retainer Kit with 12 popular size, fitting for door trim, radiator shield yoke…
- SAVE TIME AND MONEY – You can find 240PCS automotive push type retainer kit in the box and no need to go to a auto parts…
- HIGH QUALITY – High quality material with heavy-duty construction for durability, this push type retainers set would not…

- Better Than OEM Fender Clips – universal 8mm plastic fender clips body rivets replacement for utv atv. this set of push …
- Solid fender fastener rivets – used to hold fender and body panel on commander/maverick/outlander, polaris sportsman atv…
- Nylon Material, No Break – Solid fender fastener rivets made of high quality nylon, will not break during use. Easy to r…

- PACKAGE INCLUDE: 200PCS Nylon Fastener Rivet Clips.
- DURABLE & EASY STORAGE: Nylon Bumper Fastener Rivet Clips Made of high-quality heavy-duty Plastic material. No break or …
- Compatibility widely: Retainer clips fasteners are mainly suitable 8mm-10mm 5/16 holes and come in a stylish black color…

- These are widely used for car fenders, bumpers, doors, side skirts or other car surfaces. They can be used on motorcycle…
- Size: Hole Diameter – 8mm/0.31 inches; Stem Length – 20mm/0.78 inches; Total Length – 22mm / 0.86 inches; Diameter – 18m…
- Other Name: Car Plastic Trim Boot Rivets, Push Clip Fastener Hole, Push Retainer Bumper Fender Shield Clips, Automotive …

- Product includes: 60pcs white tree rivet fasteners, the quantity is enough for your daily use.
- Dimensions: 22.7 x 18mm/0.89 x 0.7in, top diameter is 18 mm, suitable for 1/4 inch or smaller holes.
- The fastener is made of high-quality plastic nylon material, which is firm and reliable, not easy to wear or break, and …

- Most Commonly Used In Automotive Interior Installation
- Can Support Tension Loads
- Nylon Rivet

- Car Bumper Clips: Great Assortment Push Retainer Kit with 12 popular size for many brand vehicles. ll the necessary reta…
- 5 PCS Trim Removal Tool :Our trim removal tool set fits in any crevices and works excellent in removing exterior & inter…
- High Quality:These rivets are made of high-quality nylon material and are so strong, allowing they are very hard to defo…

- ✅ Push-In Rivet, Dome Head, 0.281 in Dia., 7/32 in L, Nylon Body, 20 PK, Mfr: 27QB400250N-A
- ✅ Head Type: Dome
- ✅ Material: Nylon
- Other Names(Ford):Grille Screw, Safety Switch Rivet, Rivet – Blind, Rocker Molding Rivet
- Head Diameter: 11/16″ Stem Length: 7/8” Fits Into 1/4″ Hole
- Replaces GM: 20664092 1982-, Ford: N804570S 1986-

- ✅ Push-In Rivet, Dome Head, 1/4 in Dia., 29/32 in L, Nylon Body, 25 PK, Mfr: 5935PK-A
- ✅ Head Type: Dome
- ✅ Material: Nylon
Advanced Applications and Future Innovations
Beyond conventional uses, Push-In Rivets are finding their way into advanced technological applications. In automotive manufacturing, for example, metal push rivets are used for body assembly, while in the electronics industry, plastic push rivets help secure delicate components with minimal weight. Research and development are driving innovations such as smart Push-In Rivets that integrate sensors to monitor stress and predict maintenance needs. These future-forward technologies promise to enhance the safety and performance of assemblies, making Push-In Rivets an indispensable part of modern manufacturing processes. (Source: Würth Industry USA)
Technical Analysis and Engineering Insights
A detailed technical analysis of Push-In Rivets reveals several critical performance factors:
- Tensile and Shear Strength: The strength of Push-In Rivets is largely determined by the material—stainless steel options offer superior performance, while plastic variants provide adequate strength for lightweight applications.
- Dimensional Accuracy: Uniform manufacturing processes ensure that each rivet meets strict tolerances, resulting in consistent performance across large-scale productions.
- Installation Dynamics: The force applied during installation must be carefully controlled to prevent over-expansion or incomplete seating, which can compromise the fastener’s integrity.
Engineering studies have shown that assemblies using Push-In Rivets exhibit up to a 25% improvement in joint strength compared to those using conventional fasteners, making them a reliable choice for high-demand applications. (Source: OneMonroe)
Comparative Research and Statistical Findings
Recent comparative studies have highlighted the advantages of Push-In Rivets over other fastening methods. One study published in the Journal of Fastener Engineering found that installations utilizing Push-In Rivets achieved a 22% higher shear strength than traditional rivet types. Additionally, field data indicates that the streamlined installation process of Push-In Rivets can reduce production time by approximately 30%, translating to significant cost savings in large-scale manufacturing environments. These statistics underscore the value of investing in high-quality Push-In Rivets for both industrial and DIY projects. (Source: OneMonroe)
Practical DIY Strategies for Using Push-In Rivets
For DIY enthusiasts, Push-In Rivets offer an accessible and efficient solution for various projects. Here are some actionable strategies:
- Use a Drill Guide: Ensure uniformity and precision by employing a drill guide for accurate hole placement.
- Choose the Right Rivet Size: Consult manufacturer specifications to match the rivet size with your material thickness.
- Invest in a Quality Installation Tool: A reliable, battery-operated tool can simplify the process and reduce manual effort.
- Practice on Scrap Material: Test your technique on sample materials before tackling your main project.
- Inspect Every Installation: After fastening, verify that the Push-In Rivet is fully seated and that its expansion provides a secure lock.
These strategies help achieve consistent, high-quality results, making your projects both durable and aesthetically pleasing. (Source: Albany County Fasteners)
Sustainability and Environmental Considerations
Sustainability is increasingly important in today’s fastener market. Many manufacturers now produce Push-In Rivets using recyclable materials and environmentally friendly processes. For instance, recycled plastic push rivets offer a sustainable option without compromising performance, while green-certified metal push rivets are favored for their long-lasting durability. By choosing eco-friendly Push-In Rivets, you not only ensure robust assembly performance but also contribute to reducing your project’s environmental footprint. (Source: Würth Industry USA)
Global Market Impact and Economic Outlook
The global demand for efficient and reliable fasteners like Push-In Rivets is on the rise. Economic reports indicate that the fastener market is experiencing robust growth, driven by increased investments in automotive, aerospace, and electronics manufacturing. Emerging markets in Asia and Europe are showing a marked preference for advanced fastening solutions, including Push-In Rivets, due to their streamlined installation and high performance. This upward trend suggests that investing in premium Push-In Rivets now will yield long-term benefits in both quality and cost efficiency. (Source: Albany County Fasteners)
User Reviews and Field Testimonials
Feedback from professionals and DIY users alike consistently highlights the advantages of Push-In Rivets. Engineers have reported that using Push-In Rivets in assembly lines has not only enhanced joint strength but also reduced installation time significantly. Numerous case studies show that products like plastic push rivets and metal push rivets receive high marks for their ease of use and reliability. These testimonials reinforce the notion that investing in high-quality Push-In Rivets is a smart choice for ensuring durable, long-lasting assemblies in a wide range of applications. (Source: Würth Industry USA)
Future Outlook and Innovative Trends in Fastening Technology
The future of Push-In Rivets is bright, as ongoing innovations promise to revolutionize fastening technology. Emerging developments include smart fasteners equipped with sensors to monitor joint integrity and predict maintenance needs. These advanced Push-In Rivets are expected to become a staple in industries where safety and performance are critical, such as aerospace and civil engineering. As research continues to push the boundaries of fastener technology, Push-In Rivets will undoubtedly remain at the forefront, offering unparalleled ease of installation and structural reliability. (Source: OneMonroe)
A Valuable Investment in Modern Fastening Solutions
Choosing the right Push-In Rivets is a key decision that can enhance the durability and performance of any project. From high-demand industrial applications to everyday DIY repairs, high-quality Push-In Rivets ensure secure, reliable joints that stand up to rigorous use. Whether you opt for metal push rivets for heavy-duty applications or plastic push rivets for lighter tasks, the benefits of these fasteners are clear. The insights and data provided in this guide offer a solid foundation for making an informed choice that will pay dividends in the long run.
A Final Note on Trust and Reliability
The extensive research, technical analysis, and expert recommendations in this guide underscore the value of Push-In Rivets in modern assembly solutions. By understanding the various material options, installation techniques, and performance metrics, you can confidently select the best Push-In Rivets for your projects. This article is designed to serve as a trusted resource, providing you with the detailed information necessary to achieve secure, durable, and efficient fastenings. Embrace these insights and invest wisely in Push-In Rivets that promise long-lasting performance. (Source: Albany County Fasteners)
Additional Resources and Expert Citations
For further reading and detailed technical specifications on Push-In Rivets, please visit the Fasteners 101 guide and explore additional insights from Würth Industry USA. These reputable sources provide comprehensive analyses and expert reviews that can further enhance your understanding and decision-making process when it comes to choosing the best Push-In Rivets.
OUR CATEGORIES
“As an Amazon Associate we earn from qualifying purchases.”