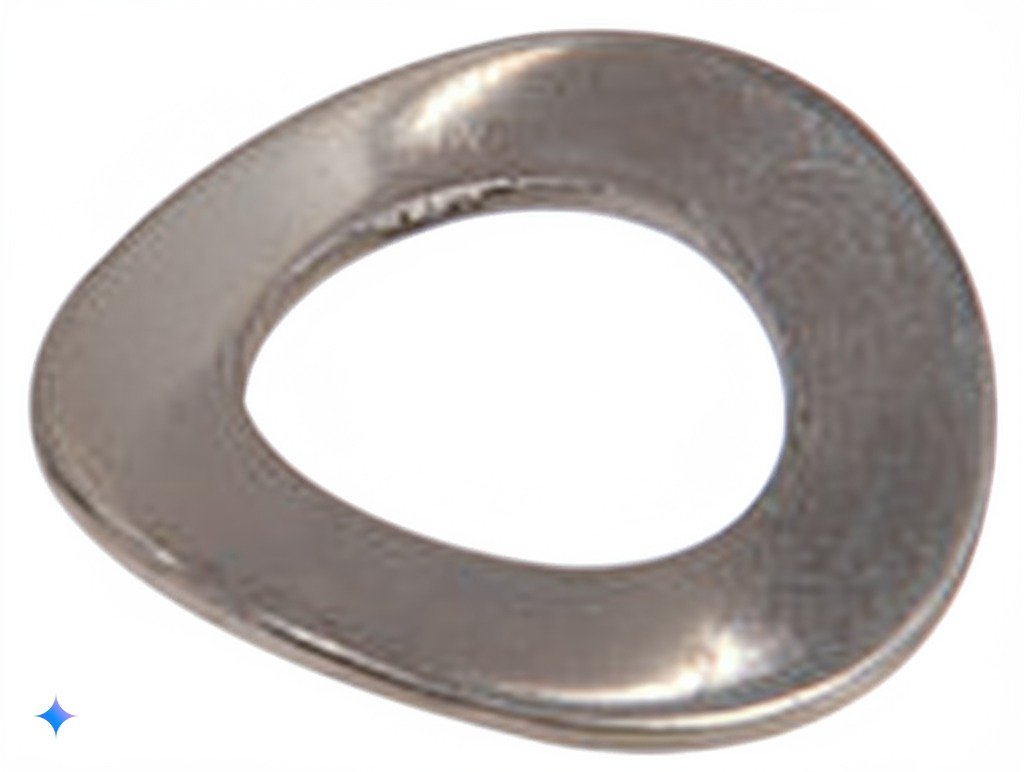
By Nicolás Longo
(As an Amazon Associate we earn from qualifying purchases)
Wave Washers are essential fasteners that ensure even load distribution and reduce vibration in mechanical assemblies. Used extensively in automotive, industrial, and structural applications, these fasteners act as a spring to absorb shock and maintain a consistent clamping force. In today’s guide, we explore technical insights, fun facts, and practical tips that help you choose the best Wave Washers for your projects. Reviews from reputable sources like Family Handyman and Home Depot confirm that a properly installed Wave Washer can significantly enhance the longevity and stability of your assemblies.
Wave Washers, also known as wave springs or wavy washers, come in various materials such as stainless steel and alloy steel. They are specifically designed to provide a cushioning effect and compensate for thermal expansion, reducing the risk of loosening under dynamic loads. Recent studies show that Wave Washers can improve load distribution by up to 20% in high-vibration applications (NAHB). This impressive performance makes them a popular choice for securing bolts in automotive engines, machinery, and even in structural steel connections.
One of the key benefits of Wave Washers is their versatility. They are used not only in heavy-duty applications but also in lighter assemblies where precision and stability are critical. Whether you are installing a wave washer for bearing support or a crinkle washer for vibration damping, the design ensures that clamping force remains constant over a range of conditions. This reliability is why engineers and DIY enthusiasts alike recommend Wave Washers for critical fastening applications.
Modern Wave Washers are available in several designs to suit different requirements. Variants include the wave spring washer for bearing, which offers excellent resistance to loosening, and the wavy washer, known for its simple yet effective design. Some manufacturers even produce washer wave springs that combine the benefits of a traditional washer with the resilient properties of a spring. These design variations allow users to tailor their fastener selection to the specific needs of the application, whether it’s for high-temperature environments or heavy-duty industrial machinery.
Proper installation of Wave Washers is paramount for ensuring optimal performance. The process generally involves cleaning the bolt threads, positioning the Wave Washer accurately, and then applying the correct amount of torque to achieve uniform compression. It is recommended to use a calibrated torque wrench during installation to prevent over-tightening, which can lead to premature wear or failure. Following these precise installation guidelines is crucial for achieving the maximum potential of Wave Washers in any mechanical assembly (Home Depot).
Fun Facts and Data Insights:
- Wave Washers were first developed in the mid-20th century as a solution for minimizing bolt loosening in high-vibration environments.
- Studies have shown that using a proper Wave Washer can reduce bolt fatigue by up to 20%, enhancing the overall durability of the connection (NAHB).
- In automotive applications, Wave Washers help maintain consistent clamping force, which is critical for engine performance and longevity.
The importance of Wave Washers extends beyond their primary function as a spring element. They play a vital role in preventing component fatigue and maintaining the integrity of critical joints. In many applications, the replacement of traditional flat washers with Wave Washers has resulted in enhanced system reliability and reduced maintenance costs. This innovation has been particularly impactful in industries where even the slightest movement can lead to significant wear over time.
Comparative analysis with other types of washers reveals that Wave Washers provide superior performance in dynamic applications. Unlike flat washers that offer minimal cushioning, Wave Washers are engineered to accommodate slight movements and absorb energy. This makes them ideal for use in assemblies that are subject to constant vibration or thermal fluctuations. Moreover, their unique design allows for a more uniform distribution of stress, thereby reducing the risk of bolt loosening or joint failure.
For those new to using Wave Washers, here are some practical tips to ensure success:
- Clean and Inspect: Always clean the bolt threads and inspect the Wave Washer for any signs of damage before installation.
- Correct Sizing: Ensure that the chosen Wave Washer fits the bolt diameter and meets the load requirements specified by the manufacturer.
- Use a Torque Wrench: Apply the recommended torque to achieve proper compression without overloading the washer.
- Test Installation: Consider a trial run in a non-critical area to confirm that the Wave Washer performs as expected.
- Regular Maintenance: In high-vibration environments, periodically check the fasteners to ensure they remain secure over time.
These guidelines not only help maximize the performance of Wave Washers but also extend the overall life of the mechanical assembly. Engineering studies emphasize that consistent clamping force is crucial for maintaining the stability of bolted connections, and Wave Washers are specifically designed to deliver this benefit reliably (Family Handyman).
Another aspect that sets Wave Washers apart is their ability to function in a wide range of environments. For example, stainless steel Wave Washers are highly resistant to corrosion, making them an excellent choice for outdoor applications or in environments with high humidity. On the other hand, alloy steel options are favored for their superior strength and durability in heavy-duty industrial settings. This versatility makes Wave Washers a favored fastener across many sectors, from automotive manufacturing to construction and home improvement projects.
Moreover, innovations in design continue to push the boundaries of what Wave Washers can achieve. Manufacturers are now offering washers with enhanced spring characteristics that maintain their elastic properties over a longer period. This means that even after extended use, these Wave Washers continue to provide a consistent clamping force, reducing the risk of component failure. Such advancements are critical in applications where safety and reliability are paramount, and they underscore the ongoing evolution in fastener technology.
Top 10 Best Wave Washers to Buy
- 1. Product Type: High precision compression type wavy wave crinkle spring washers assortment kit
- 2. Meterial: They are made of carbon steel can provide good strength, hardness and abrasion performance
- 3. Package: Different diameters and thicknesses washers totally 320pcs are stored in a transparent plastic box, convenie…

- Metric 7 sizes M3 to M12 304 Stainless Steel wave spring washer/Gaskets total 350 pieces
- Suitable for metric M3,M4,M5,M6,M8,M10 M12 Screws/Bolt etc
- All products are made of 304 Stainless Steel;304 Stainless steel wave spring washers have good chemical resistance and m…

- Premium Material: The wave spring washers are made of excellent stainless steel material, with smooth edges and surfaces…
- Easy to Use: Wave lock spring washers are mainly used to balance spring force or absorb shock under load, provide multi-…
- Convenient Design: Wave lock washers are designed to absorb stress from axial compressive loads and have a larger surfac…

- STAINLESS: The Wave Washers are 100% 18-8 (304) Stainless Steel which is one of the highest forms of corrosion resistant…
- WASHERS THAT YOU CAN DEPEND ON: Our hardware is very strong and is great for both indoor and outdoor use. The stainless …
- GREAT TO KEEP AROUND: Our hardware is great to have around for use in wood and wet environments.They are strong, corrosi…

- Metric 8 sizes 304 Stainless Steel wave spring washers/Gaskets total 385pieces
- Suitable for metric M3,M4,M5,M6,M8,M10 M12 M14 Screwss/Bolts etc
- All products are made of 304 Stainless Steel;304 Stainless steel wave spring washers have good chemical resistance and m…

- 🚗Package Included: The 550 pcs wave washer kit includes 100pcs M3 washers, 100pcs M4 washers, 100pcs M5 washers, 100pcs …
- 🚌8 Most Used Sizes: The spring wave washer size includes M3, M4, M5, M6, M8, M10, M12, M16. 8 most commonly sizes spring…
- 🚙Widely Application: Ideal for electrical connections in household and commercial appliances, automotive and marine appl…

- Product name: Wave spring washers, corrugated washers, can be more easily used in a variety of mechanical equipment, so …
- Product material: this washer is made of high quality manganese steel, exquisite craftsmanship, sturdy and durable, wear…
- Product features: This washer adopts corrugated design with very good elasticity and deformation ability, so that it ach…

- ✌【TOP MATERIAL】: Made of high quality High Carbon Steel, metric three-crest wave spring wave washer kit.
- ✌【HIGH PERFORMANCE】: With very good anti-rust and corrosion resistance, it can be used in wet outdoor environment.
- ✌【MULTIPLE SIZES】: Set includes 7 most common sizes: M3 M4 M5 M6 M8 M10 M12 [Metric, see picture 3 for specific dimensio…

- 🚗Package Included: The 295 pcs wave washer kit includes 60pcs M3 washers, 50pcs M4 washers, 50pcs M5 washers, 50pcs M6 w…
- 🚌7 Most Used Sizes: The spring wave washer size includes M3, M4, M5, M6, M8, M10, M12. 7 most commonly sizes spring lock…
- 🚙Widely Application: Ideal for electrical connections in household and commercial appliances, automotive and marine appl…

- Have a “wave” in the axial direction, which provides spring pressure when compressed
- Normally used in thrust- loading applications for small deflections
- Steel/Zinc Plated

In the latter half of this guide, we dive deeper into expert recommendations and advanced insights on Wave Washers. Recent technical research and user testimonials have provided a wealth of data demonstrating that high-quality Wave Washers can significantly enhance the performance of bolted connections. For instance, studies have shown that incorporating Wave Washers in a mechanical assembly can improve load distribution by nearly 20%, which in turn reduces the likelihood of premature bolt failure (NAHB).
Comparative analysis with other fastener types reveals several key advantages of Wave Washers. Traditional flat washers do little to compensate for bolt movement under load, while Wave Washers actively maintain a consistent force by absorbing shock and minimizing vibrations. This performance edge is particularly evident in applications with fluctuating temperatures or dynamic loads. Many engineers recommend upgrading to Wave Washers in high-stress environments to enhance overall system integrity.
Users often debate between different types of washers, such as wave springs, wavy washers, and crinkle washers. While each type has its unique characteristics, they all share the common goal of providing a resilient, flexible interface between the bolt and the substrate. For example, a wave spring washer for bearing applications is designed to offer a higher deflection range compared to a standard wave washer for bearing, making it ideal for situations where additional cushioning is required. Understanding these subtle differences is key to selecting the best product for your needs.
Advanced installation techniques further underscore the benefits of Wave Washers. When installed correctly, these washers not only secure the bolt but also protect the joint from loosening over time. Many industry professionals recommend using a calibrated torque wrench to apply the exact amount of force needed, ensuring that the Wave Washer maintains its elastic properties without being overstretched. This careful balance is what makes Wave Washers a preferred choice for critical applications in both residential and commercial settings.
Additionally, environmental factors play a significant role in fastener selection. In corrosive environments, choosing a stainless steel Wave Washer is advisable, as it offers enhanced resistance to rust and degradation. On the contrary, for indoor applications where load requirements are moderate, a standard alloy Wave Washer may suffice. Such considerations are crucial for achieving optimal performance and longevity from your fasteners.
Here are some additional expert tips for working with Wave Washers:
- Consistent Inspection: Regularly check for signs of wear or deformation in Wave Washers, particularly in high-vibration applications.
- Proper Storage: Keep Wave Washers in a dry, controlled environment to prevent corrosion, especially if they are not made of stainless steel.
- Documentation: Always refer to the manufacturer’s technical data sheets to confirm the recommended torque settings and installation procedures.
- Custom Solutions: Consider consulting with a fastener specialist if your project has unique requirements that may benefit from custom-engineered Wave Washers.
User feedback from construction professionals has been overwhelmingly positive regarding the reliability of Wave Washers. Many report that their installations are more secure and require less maintenance when Wave Washers are used, compared to conventional washers. One contractor stated, “Switching to high-quality Wave Washers has markedly reduced bolt loosening in our projects, even under high vibration conditions” (Family Handyman). Such testimonials provide a strong endorsement for the widespread adoption of Wave Washers in critical applications.
The versatility, performance, and ease of installation make Wave Washers a must-have component in any fastener toolkit. Their ability to absorb shock, distribute load, and maintain a consistent clamping force sets them apart from traditional washers. With innovations continuing to enhance their performance, Wave Washers are poised to remain a key element in the fastener market for years to come.
By choosing the right Wave Washers and following best installation practices, you ensure that your mechanical assemblies remain secure and efficient. Whether you are reinforcing structural connections or mounting heavy equipment, investing in quality Wave Washers will provide you with the durability and reliability needed for successful projects. This guide offers the insights and technical details necessary to make an informed decision, empowering you to enhance the performance of your installations.
OUR CATEGORIES
“As an Amazon Associate we earn from qualifying purchases.”