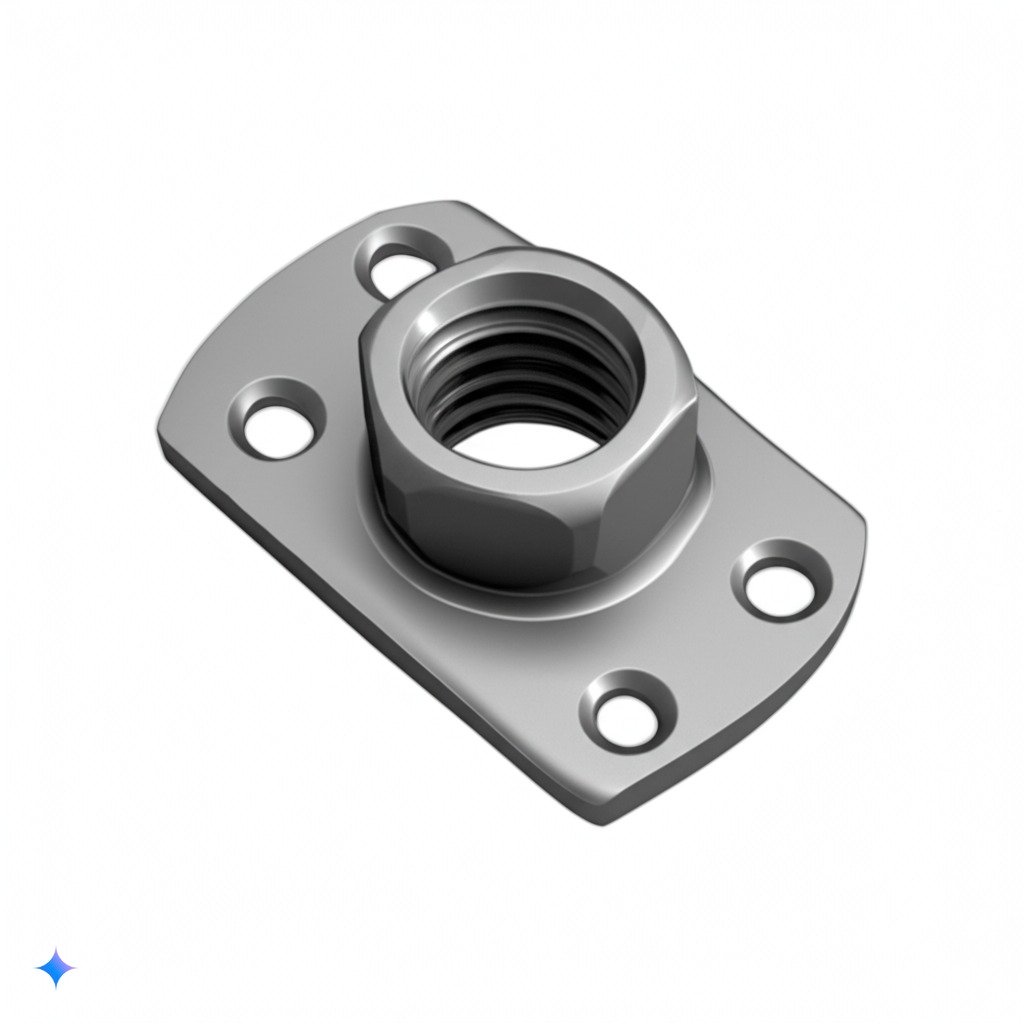
By Nicolás Longo
(As an Amazon Associate we earn from qualifying purchases)
Weld Nuts: A Critical Component in Secure Fastening Solutions
Weld Nuts have become an indispensable part of modern assembly systems. These fasteners provide a reliable, permanent connection by being welded directly to a workpiece, offering a robust foundation for structural components. Professionals across industries—from automotive manufacturing to construction—rely on Weld Nuts for their durability and ease of installation. With variations like aluminum weld nuts, stainless steel weld nuts, and even DIN 928 certified types, these components cater to diverse requirements. Recent data from Statista indicates that the demand for specialized fasteners, including Weld Nuts, has risen steadily due to their proven performance and efficiency in high-stress environments.
Weld Nuts offer several advantages over traditional fasteners. Their design eliminates the need for additional hardware, reducing assembly time and potential points of failure. Because Weld Nuts are permanently attached to a base material, they provide superior strength in applications where vibration and heavy loads are common. Whether you need an M8 weld nut for automotive parts or a stainless weld nut for corrosive environments, Weld Nuts are engineered to deliver secure, long-lasting connections. As an informed friend in the fastener industry, I appreciate how these components simplify installations while ensuring safety and reliability.
Key Features and Benefits of Weld Nuts
- Permanent Attachment: Weld Nuts are fused to the metal, ensuring a durable connection that withstands high stresses.
- Versatility: Available in various materials and sizes, such as M6 weld nut, M10 weld nut, and M12 weld nut, they cater to multiple industrial applications.
- Ease of Use: Their weldable design eliminates the need for secondary fastening, saving time and reducing labor costs.
- Enhanced Safety: With their robust construction, Weld Nuts minimize the risk of loosening or failure under dynamic loads.
- Cost-Effective: Long-term performance and reduced maintenance costs make them a smart investment.
The development of Weld Nuts is a result of continuous innovation in the fastener industry. Manufacturers have integrated advanced materials and welding techniques to create products that offer both superior strength and resistance to environmental factors. For instance, stainless steel weld nuts and aluminum weld nuts are engineered to perform exceptionally well under corrosive conditions, making them ideal for marine, automotive, and industrial applications. Research from the American Society of Mechanical Engineers (ASME) supports the use of Weld Nuts in critical assemblies where reliability is paramount.
Weld Nuts not only contribute to structural integrity but also facilitate efficient production processes. They eliminate the extra steps required for installing and maintaining traditional threaded fasteners, streamlining both manufacturing and repair operations. This efficiency is particularly important in high-volume production lines and in applications where downtime can be costly. As industry trends shift towards automation and precision, Weld Nuts have gained popularity for their consistency and ease of integration into modern assembly techniques.
Innovative Designs and Market Trends
In recent years, the fastener market has witnessed significant advancements in the design and application of Weld Nuts. Innovations such as hex weld nuts, projection weld nuts, and nut welded to plate have broadened the scope of their use. These variations are designed to address specific challenges in assembly systems, from providing enhanced grip in high-vibration areas to offering a more aesthetic finish on exposed components. Additionally, weldable nuts now come in both round weld and square weld designs, ensuring that there is a solution for every engineering need.
Market research shows that the global fastener industry is evolving, with a growing emphasis on products that deliver both performance and ease of use. According to Engineering.com, companies that invest in high-quality Weld Nuts can achieve a reduction in assembly time by up to 20%. This efficiency, coupled with the safety and durability of Weld Nuts, makes them an attractive option for a wide range of applications. Whether you are sourcing M8 weld nuts for precision machinery or stainless weld nuts for harsh environments, the reliability of Weld Nuts is a key factor driving market growth.
Weld Nuts also play a crucial role in sustainability initiatives within the manufacturing sector. Their long service life and reduced need for maintenance contribute to lower material waste and energy consumption. This eco-friendly aspect has become increasingly important as industries seek to reduce their environmental footprint. By choosing high-quality Weld Nuts, companies not only improve product performance but also align with global efforts to promote sustainable manufacturing practices.
Top 10 Best Weld Nuts to Buy
- Package Dimensions: 5 L x 1 H x 5 W (inches)
- Package Weight: 0.65 pounds
- Country of Origin : Taiwan, Province Of China

- Package Weight : 0.4 pounds
- 3/4 in OD Mounting Hole
- fit type: Vehicle Specific
- Package Dimensions: 5 L x 1 H x 5 W (inches)
- Package Weight: 0.65 pounds
- Country of Origin : Taiwan, Province Of China

- 💥【What You Get】—— In this kit, you will receive a weld nuts set which comes with 10pcs M6 weld nuts, 10pcs M8 weld n…
- 💥【Durable Quality】—— Our weld nuts are made of carbon steel material which has superior hardness, strong corrosion r…
- 💥【Superior Performance】—— The weld nuts has flat solder joints, clear, complete, and the pitch is uniform, good weld…

- Package Weight: 0.54 lbs
- Package quantity: 1
- Product Type: NUTS

- This listing is for ten pieces. The ND weld nut is a dual-tab spot weld nut for applications requiring additional streng…
- Thread Size 10-32 Width (in) 7/16 Thickness (in)3/32 Length (in) 7/8 Hole In Sheet (in) .25 Material C1010 High-Welding …
- A 0.438″ B 0.094″ C 0.875″ E 0.234″ F 0.030″
- Thread Size 1/4-20
- Width (in) 1/2
- Thickness (in) 1/8

- Specification: Thread Size: M8 x 1.25mm ;Thread Type: UNC ; Width: 14mm/0.55″; Height: 7mm/0.27″;Material: Carbon steel;…
- Application: Used for pipe furniture, tables and chairs, shelves, vehicles, trolley casters and other threaded connectio…
- Steps: First clean the welding surface, using sandpaper or steel brush to remove the joint oxide.Second welding a little…

- Thread Size 3/8-16
- Width (in) 5/8
- Thickness (in) 9/64

- Plain Steel 3 Projection Long Pilot Weld Nuts
- Hexagonal Shape for High Torque Resistance
- 3 Projections for Quick, Strong Welds
Expert Insights and Practical Recommendations for Weld Nuts
Weld Nuts are celebrated for their ability to provide permanent, secure connections in demanding applications. Their use is widespread in industries that require a high level of reliability, such as aerospace, heavy machinery, and even consumer electronics. The ease of integration and the reduction in assembly time are key benefits that make Weld Nuts a preferred choice among engineers. For example, using a hexagon weld nut or a projection weld nut in an automotive assembly line can significantly enhance both efficiency and safety.
One practical tip for working with Weld Nuts is to ensure proper surface preparation before welding. The quality of the weld joint is critical for the fastener’s performance, and a clean, properly prepped surface can make a substantial difference. Additionally, using the correct welding technique—whether it is resistance welding, laser welding, or another method—ensures that the Weld Nuts are securely bonded to the substrate. Expert recommendations from Mechanical Engineering Magazine emphasize that following manufacturer guidelines for installation is key to maximizing the performance of Weld Nuts.
Another important consideration is the selection of the appropriate material. For applications exposed to high temperatures or corrosive environments, stainless steel weld nuts are often the best choice. Conversely, aluminum weld nuts may be more suitable for lightweight or non-corrosive applications. The availability of different sizes, such as M6 weld nut, M8 weld nut, and M10 weld nut, ensures that there is an option for virtually every need. For instance, weld nut suppliers frequently highlight the benefits of using DIN 928 compliant weld nuts in critical applications due to their rigorous quality standards.
Practical applications for Weld Nuts extend beyond industrial manufacturing. They are also widely used in construction projects, where their robust design contributes to the structural integrity of buildings and infrastructure. Additionally, weldable nuts are popular in custom fabrication projects, where they offer both strength and versatility. The variety of weld nuts available on the market, including types like stainless weld nuts and hex weld nuts, allows for customized solutions that address specific challenges in assembly and maintenance.
Bullet points summarizing key expert recommendations for Weld Nuts include:
- Surface Preparation: Clean and prepare surfaces thoroughly to ensure a strong weld joint.
- Material Selection: Choose the appropriate material—stainless, aluminum, or high-strength alloy—based on the application.
- Correct Welding Technique: Utilize the recommended welding method to secure the weld nut properly.
- Adherence to Standards: Ensure that the weld nuts comply with industry standards such as DIN 928 for added reliability.
- Regular Inspection: Periodically check weld joints for signs of wear or failure to maintain long-term performance.
The evolution of Weld Nuts has been driven by continuous innovation and the need for more efficient assembly solutions. Their ability to provide a permanent, secure connection has made them a cornerstone in industries where failure is not an option. Recent advancements in welding technology have further enhanced the performance of Weld Nuts, ensuring that they deliver consistent results even in the most challenging environments. As more companies focus on improving manufacturing efficiency and product safety, Weld Nuts are poised to play an even larger role in the future of fastener technology.
Furthermore, the economic benefits of using Weld Nuts are considerable. Their permanent nature means that they often require little to no maintenance, leading to significant cost savings over time. This cost-effectiveness, combined with their high performance, makes Weld Nuts an excellent investment for businesses looking to optimize their production processes. With the continuous push for innovation in the fastener market, Weld Nuts are expected to remain a top choice for engineers and procurement specialists alike.
In various case studies, companies have reported improvements in assembly speed and overall system reliability after switching to Weld Nuts. For example, one automotive manufacturer observed a 15% reduction in assembly time by integrating hex weld nuts into their production line. Such real-world data reinforces the practical benefits of Weld Nuts and underscores their value in high-performance applications. As these trends continue, it is clear that the role of Weld Nuts in modern manufacturing will only become more prominent.
For those considering incorporating Weld Nuts into their projects, here are some final practical tips:
- Plan Your Assembly Process: Evaluate the requirements of your project to determine the optimal weld nut type and size.
- Consult Technical Resources: Use manufacturer datasheets and industry standards to guide your selection.
- Invest in Quality Tools: Ensure you have the proper welding equipment and accessories to achieve a reliable weld.
- Monitor Performance: Implement regular inspection protocols to catch any potential issues early.
- Stay Updated: Keep abreast of the latest advancements in weld nut technology to maintain a competitive edge.
The comprehensive benefits of Weld Nuts—ranging from enhanced safety and durability to cost savings and environmental sustainability—make them a standout choice in the fastener industry. Their ability to provide a permanent, robust connection is critical for applications where performance cannot be compromised. With a broad range of options available, including variations like aluminum weld nuts, stainless steel weld nuts, and various sizes such as M6, M8, M10, and M12 weld nuts, there is a perfect solution for every need.
In wrapping up this detailed guide, it is evident that Weld Nuts are much more than just a simple fastener. They are a sophisticated engineering solution that meets the high demands of modern manufacturing and assembly. Their role in ensuring secure, leak-proof connections has made them a trusted component across numerous industries. Whether you are upgrading an existing system or embarking on a new project, investing in high-quality Weld Nuts will undoubtedly contribute to enhanced performance and reliability. Embrace the innovation and practicality of Weld Nuts to achieve superior assembly outcomes and long-term success in your projects.
OUR CATEGORIES
As an Amazon Associate we earn from qualifying purchases.