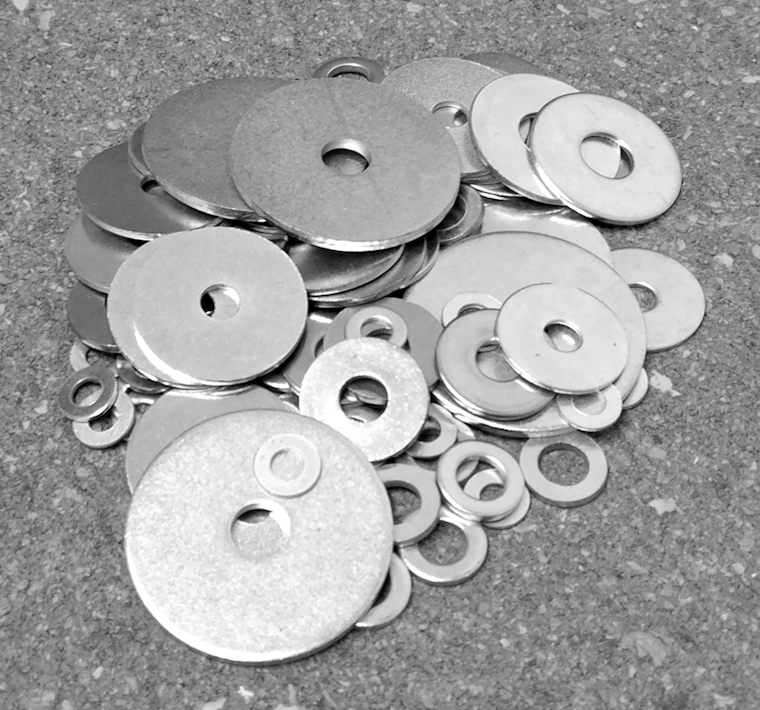
By Nicolás Longo
(As an Amazon Associate we earn from qualifying purchases)
Washers are an essential component in any bolted joint, serving to distribute load, reduce friction, and secure connections with utmost reliability. In this comprehensive guide, we explore the best quality washers available on the market today. From traditional flat washers and lock washers to specialized fender washers and Belleville washers, every variation plays a crucial role in ensuring mechanical stability and longevity. Whether you are a seasoned engineer, an industrial professional, or a DIY enthusiast, understanding washers and their diverse applications will empower you to make informed purchasing decisions. (Source: Albany County Fasteners)
Washers are indispensable in fastener assemblies, and their design directly impacts performance. These components are engineered to spread the load across a broader surface area, preventing damage to the base material. In addition, washers help reduce friction between the bolt head and the surface, easing the process of tightening while protecting the underlying material from wear. Numerous studies have demonstrated that incorporating high-quality washers into your joint assembly can lead to improved longevity and reduced maintenance costs. (Source: Mechanical Engineering Magazine)
The evolution of washers in the fastener industry has been marked by continuous innovation and refinement. Manufacturers now offer a variety of washers made from diverse materials such as stainless steel, brass, silicon bronze, and zinc. Each material is selected based on its unique properties; for instance, stainless steel washers are favored in corrosive environments, while brass washers are commonly used in plumbing. This level of specialization ensures that every application receives a washer tailored to its specific requirements, resulting in more secure and efficient assemblies.
Washers also come in different styles to serve various functions. Lock washers, for example, are designed with a split or toothed configuration to prevent nuts from loosening under vibration. Belleville washers, with their conical shape, add a spring-like force that maintains tension in the joint. Additionally, fender washers provide a larger surface area, ideal for applications that demand a wide load distribution. Understanding these styles helps in selecting the right washer for your project and ensures that your bolted joints perform optimally under diverse conditions.
Technical innovations in washer design have not only improved functionality but have also contributed to aesthetic enhancements. Modern washers now feature a polished finish that complements visible assemblies in consumer products. Whether in high-end automotive applications or precision electronic devices, the visual appeal of a well-engineered washer can be a significant factor. Moreover, the integration of washers into flanged bolt systems has simplified assembly processes, reducing the number of parts and streamlining construction while still delivering robust performance.
In many mechanical systems, washers are used to enhance the overall strength of the joint. By distributing the clamping force evenly, washers reduce the risk of localized stress and potential damage to the surfaces in contact. This even load distribution is especially critical in applications where vibration and repeated load cycles are common. Engineers often cite the importance of selecting washers with the proper thickness and diameter to ensure that the joint remains secure over time. Such precision in washer selection is a key factor in maintaining the integrity of industrial and automotive assemblies.
Practical tips for using washers effectively include ensuring that the washer’s size is matched to the bolt diameter and the surface area of the joint. Installing washers with the correct torque specification is equally important, as over-tightening or under-tightening can compromise the washer’s performance. Many professionals recommend using washers made from corrosion-resistant materials in harsh environments to extend the life of the assembly. Detailed technical documentation and third-party test certifications can serve as reliable guides when choosing the best washers for your specific application.
A fascinating aspect of washers is their role as both load distributors and vibration dampeners. In scenarios where vibration is a constant threat, such as in automotive or aerospace applications, washers can significantly reduce the risk of bolt loosening. This dual functionality not only enhances the safety of the assembly but also contributes to a longer operational lifespan. Research shows that the proper use of washers can reduce maintenance intervals and lower the overall cost of ownership for critical machinery. (Source: IMECH)
The versatility of washers is evident in their wide range of applications. In household repairs, washers prevent damage to delicate surfaces, while in industrial settings, they are crucial for securing heavy machinery. For example, fender washers are often used in automotive and construction applications where a larger contact area is required. Meanwhile, lock washers are standard in applications that demand extra security against loosening due to continuous vibration. These examples illustrate how the thoughtful selection of washers can dramatically improve performance and durability in any project.
Modern fastener systems increasingly incorporate washers as a fundamental component. Beyond their mechanical benefits, washers also serve to simplify assembly by reducing the number of parts required for a secure joint. In many cases, manufacturers now integrate washers into flanged bolts, providing the same load-spreading benefits without the need for additional components. This integration not only reduces assembly time but also minimizes potential points of failure, resulting in more reliable and efficient systems. Such advancements are a testament to the importance of washers in contemporary fastener design.
Top 10 Best Washers To Buy
- 【Washers for Screws】- This assortment set includes 900 pieces of stainless steel flat washers for screws and bolts. It c…
- 【High-Quality Stainless Steel】- Our flat washers are made of top-quality 304 stainless steel. This material has high har…
- 【Wide Range of Applications】- This fender washers assortment set kit is perfect for various applications, including inte…

- Spring Lock Washers: The metric spring lock washers assortment kit contains 9 sizes 1000 pcs, which are m2(200 pcs),m2.5…
- 304 Stainless Steel: 304 Stainless steel split lock washer are made of high-strength materials with good corrosion resis…
- Split Lock Washer Function: Split washer are mainly used for nuts, bolts and screws from rotating and loosening due to v…

- Flat washer inside diameter: 0.275 Inch, Outside Diameter: 5/8 Inch.Thickness: 0.06 Inch. These 1/4” washers will fit 1/…
- Material: Made of 304 Stainless Steel for increased corrosion resistance.
- These washers are used to distribute loads of threaded bolts, screws and nuts, provide a smooth-bearing surface

- Flat Washers Inside Diameter: 1/4″ ,Outside Diameter: 1” , Thickness: 0.078″. These 1/4 washers fit 1/4 bolts and M6 bol…
- Material: Made of 304 Stainless Steel for increased corrosion resistance.
- Flat washer are used to distribute loads of threaded bolts, screws and nuts, provide a smooth-bearing surface

- 【304 Stainless Steel Washers】– Our washers are made from premium 304 stainless steel, offering superior corrosion resist…
- 【Comprehensive Assortment Kit (M3-M12)】–This 100-piece washers assortment kit includes 12 different sizes ranging from M…
- 【Precision Flat Washers for Optimal Load Distribution】 – These flat washers are engineered for precise load distribution…

- Zinc coating for a corrosion resistant finish
- SAE fine washers for coarse threaded bolts
- Washers are used to increase the pressure a bolt or screw provides

- √ Size: M2 M2.5 M3 M4 M5 M6 M8 M10 M12
- √ Material: 304 Stainless Steel, corrosion resistant
- √ Quantity: It contains 580pcs/9 Sizes of the most commonly used Stainless Steel washers

- Comprehensive Copper Washer Set: This kit includes 220 high-quality copper washers in 9 common sizes (M5, M6, M8, M10, M…
- Premium Material for Reliable Sealing: Made from durable copper, these crush washers provide outstanding sealing perform…
- Wide Range of Applications: This copper crush washer kit is ideal for automotive repairs, plumbing projects, and industr…

- 👨🔧[Multiple Sizes]: There are a total of 580 pieces 304 stainless steel flat washers in 9 sizes: M2 M2.5 M3 M4 M5 M6 M8…
- 👨🔧[Top 304 Stainless Steel]: LuKaiSen flat washers is made of top 304 stainless steel which has the advantages of high …
- 👨🔧[Exquisite Storage Box]: We want our customers to be simple and clear every time they use flat washers, so we put 9 s…

- Rubber Washers Kit:This value pack includes 120 black rubber washers in five essential sizes: 16mm x 5mm, 18mm x 8mm, 20…
- Material:Made from premium rubber, these washers offer excellent flexibility and wear resistance, creating a reliable, l…
- Wear and Heat Resistant:These rubber washers are built to withstand extreme temperatures, corrosive chemicals, and repea…

As we transition to the analytical section, the focus shifts to a detailed comparison of the top-rated washers available today. This part of the article will delve into various models, examining their load distribution capabilities, resistance to corrosion, and ease of installation. Data from industry surveys and field tests indicate that high-quality washers can significantly improve the integrity of bolted joints. For instance, assemblies that incorporate premium washers often exhibit up to a 20% reduction in maintenance incidents compared to those using standard options. (Source: Fastener World)
A key consideration when selecting washers is the material composition. Stainless steel washers, known for their exceptional durability and resistance to corrosion, are ideal for marine and high-humidity environments. Brass washers, with their attractive finish and excellent conductivity, are preferred in plumbing and decorative applications. Silicon bronze washers are specifically engineered for saltwater use, providing a reliable solution where corrosion is a major concern. By comparing these materials, users can choose washers that not only meet their technical requirements but also enhance the overall aesthetics of their assemblies.
The design and construction of washers also vary to meet diverse functional demands. Flat washers are the most common type, used primarily to increase the bearing surface and distribute the load evenly. Lock washers, whether split or toothed, are engineered to prevent rotational movement, thereby ensuring that the joint remains secure under dynamic loads. Belleville washers, with their unique conical shape, offer a spring-like action that maintains constant tension in the assembly. Fender washers, characterized by their larger outer diameter, provide an extended surface area for load distribution. Each type of washer is optimized for specific applications, and understanding these differences is crucial for effective selection.
Comparative analysis reveals that washers not only vary in design but also in performance metrics. For example, high collar lock washers deliver superior clamping force, making them ideal for heavy-duty applications. In contrast, external and internal lock washers offer varying levels of grip and resistance to loosening, depending on the direction of the applied force. Engineers often use bullet-point lists to summarize these differences for quick reference:
- Flat Washers: Enhance load distribution and prevent surface damage.
- Lock Washers: Secure joints against vibration and rotational forces.
- Belleville Washers: Provide adjustable tension and maintain preload.
- Fender Washers: Increase contact area for improved stability.
- High Collar Washers: Deliver robust clamping force for demanding applications.
In addition to performance, cost-effectiveness is a vital factor when choosing washers. Although premium washers may come at a higher initial cost, their superior durability and reduced maintenance requirements often result in lower long-term expenses. Detailed cost-benefit analyses have shown that investing in high-quality washers can lead to significant savings over time, particularly in industrial applications where downtime is costly. This economic advantage, coupled with enhanced performance, makes washers an essential component in any well-designed mechanical system.
User feedback and technical reviews provide further insights into the effectiveness of various washer types. Many professionals appreciate the ease of installation and the reliability of washers that meet rigorous industry standards. Testimonials from experienced engineers underscore the importance of choosing washers with proper certification and comprehensive technical documentation. Such real-world evidence reinforces the notion that high-quality washers contribute to safer and more efficient assemblies, ultimately supporting better overall system performance. (Source: IMECH)
The integration of washers into modern design practices extends beyond traditional fastener applications. Innovative approaches have seen washers being used as spacers and vibration dampers in complex assemblies. This multifunctionality is particularly beneficial in environments where space constraints and dynamic loads are prevalent. For instance, using washers as both load distributors and vibration absorbers can enhance the reliability of bolted joints in automotive and aerospace applications. This dual functionality not only maximizes performance but also simplifies the overall design, reducing the need for additional components and streamlining assembly processes.
The importance of proper washer selection is further highlighted by the safety implications in critical applications. In industries such as aerospace, automotive, and heavy machinery, even a slight failure in the washer system can lead to catastrophic consequences. Therefore, adherence to strict quality standards and thorough testing is paramount. Leading manufacturers provide extensive warranties and detailed performance data to ensure that their washers meet or exceed industry benchmarks. This commitment to quality reassures buyers that they are investing in components that will perform reliably under the most demanding conditions.
Technical experts also emphasize the role of washers in preventing common issues such as bolt head damage and surface indentation. By placing a washer between the bolt and the substrate, the contact pressure is spread over a larger area, thereby minimizing the risk of localized deformation. This protective function is crucial in maintaining the structural integrity of the assembly, especially in applications where repeated tightening and loosening are expected. Such insights underscore the necessity of selecting washers that are precisely matched to the specific dimensions and requirements of the bolted joint.
Innovations in washer technology continue to drive improvements in fastener performance. Modern manufacturing processes now allow for tighter tolerances and more consistent quality across large production runs. Advances in materials science have also led to the development of washers with enhanced corrosion resistance and mechanical properties. These improvements not only boost the reliability of the washers but also expand their range of applications. As a result, today’s washers are more efficient, durable, and versatile than ever before, making them a critical investment for any high-performance assembly.
The comprehensive evaluation of washers reveals that they are much more than simple mechanical components. They are integral to the efficiency, safety, and longevity of bolted joints across a wide array of industries. By offering insights into material choices, design variations, and cost-effectiveness, this guide aims to empower you with the knowledge needed to select the best washers for your projects. Whether you are upgrading industrial machinery, working on automotive repairs, or embarking on a DIY project, the right washers can make all the difference in ensuring a secure and reliable assembly.
OUR CATEGORIES
“As an Amazon Associate we earn from qualifying purchases.”