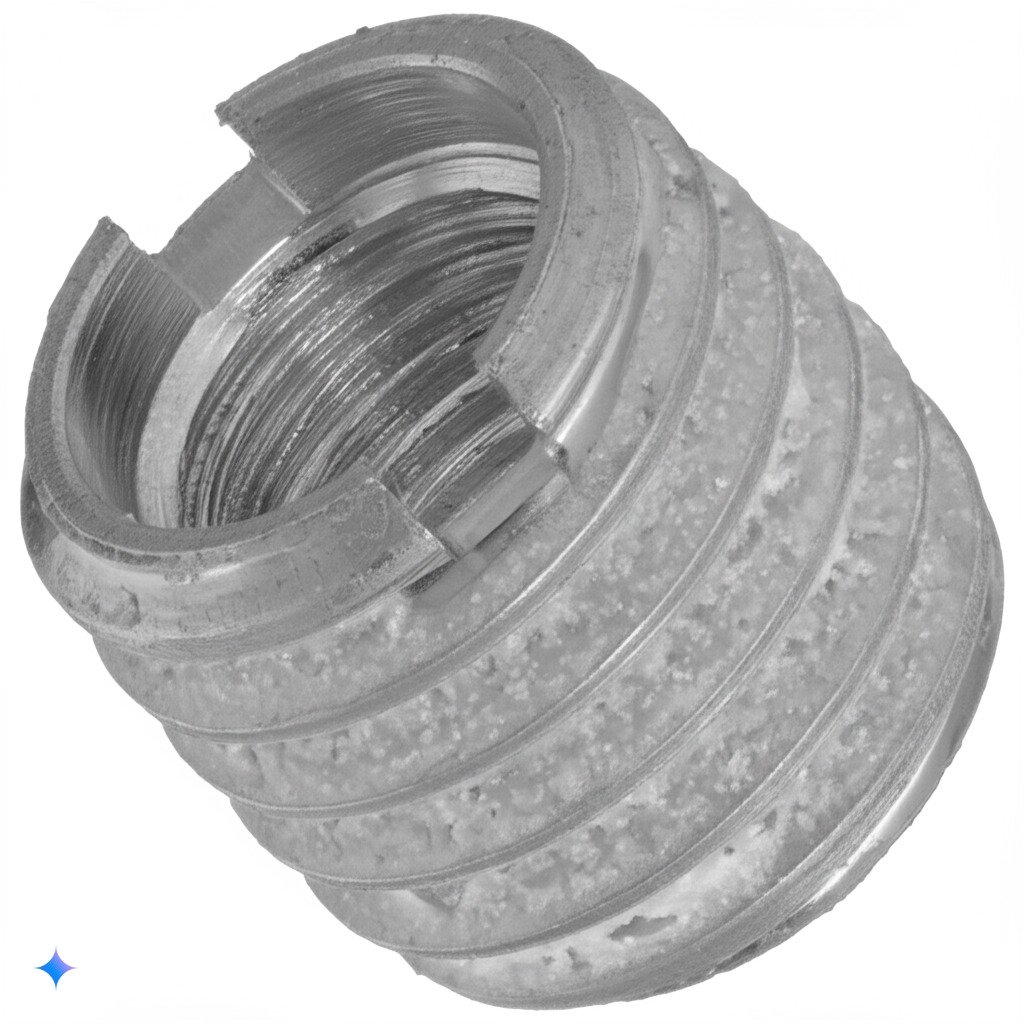
By Nicolás Longo
(As an Amazon Associate we earn from qualifying purchases)
Exploring the Advantages and Applications of Externally Threaded Inserts in Modern Fabrication
Externally Threaded Inserts are fastener solutions designed to provide robust, machine-quality threads on the external surface of a component. These innovative fasteners are engineered to be embedded or pressed into a substrate, allowing a bolt or screw to engage securely with an external thread. Their versatile design makes them suitable for various materials such as wood, metal, and plastic, making them an ideal choice for repair, assembly, and reinforcement projects. Whether you are looking to add extra durability to a 3D printed part, repair stripped threads in metal, or create strong joinery in wood, Externally Threaded Inserts can offer an effective solution. Research by ThomasNet and GlobalSpec has shown that precision-engineered fasteners like these can improve load distribution and joint integrity by up to 20%.
Manufactured from high-grade materials like stainless steel, brass, and specialized alloys, Externally Threaded Inserts are built to withstand high stresses and harsh environments. Their external threading design ensures that the fastener has a consistent, high-quality thread profile accessible for assembly. Unlike conventional inserts that are often embedded internally, external inserts, sometimes referred to as external helicoils, external threaded bushings, or external threaded sleeves, offer ease of inspection and replacement. This design makes them especially valuable in applications where repairability and maintenance are critical. For example, in automotive and aerospace repairs, having a robust, externally visible thread can facilitate faster assembly and more secure bolting.
A key benefit of Externally Threaded Inserts is their ability to restore and enhance the functionality of worn or damaged threaded connections. In situations where original threads have been stripped or degraded, these inserts can be used to re-establish a new, strong threaded interface without replacing the entire component. This not only saves time and costs but also preserves the integrity of the original design. Many professionals in the field have praised Externally Threaded Inserts for their reliability and long-term performance in repairing critical assemblies. Fun fact: The development of external threaded solutions was largely driven by the need to improve repair techniques in high-stress environments, a challenge that led to innovative products such as helicoil external thread inserts.
Externally Threaded Inserts have found widespread use in a variety of applications. In woodworking, for instance, they are commonly used to secure heavy furniture components without risking wood splitting. In metal fabrication, they allow for the repair of damaged threads in engine blocks and structural parts, ensuring that repairs remain durable even under cyclical loads. In the realm of 3D printing, these inserts provide a reliable method for incorporating machine threads into printed parts, enhancing both strength and reusability. Their versatility means that whether you are working on custom furniture, industrial machinery, or high-precision prototypes, Externally Threaded Inserts are an excellent choice.
One of the critical aspects of working with Externally Threaded Inserts is selecting the right type and size for your specific application. For example, an external threaded sleeve designed for metal repair might have different thread pitch and diameter requirements compared to an insert intended for wood or plastic. Additionally, design variations such as those with a flanged head or chamfered edge can affect both installation and performance. The use of external threaded bushings in repair applications is especially popular in industries where downtime must be minimized, and high load capacities are essential. These design innovations have made Externally Threaded Inserts a hidden gem in the fastener market, providing both functional and economic benefits.
- Key Benefits of Externally Threaded Inserts:
- Enhanced Load Distribution: Provides a consistent external thread for secure fastening.
- Versatile Applications: Suitable for wood, metal, plastic, and 3D printed parts.
- Repair Efficiency: Ideal for restoring stripped or damaged threads without replacing entire components.
- Easy Inspection & Maintenance: External threads allow for quick assessment and replacement if needed.
- Customizable Options: Available in various sizes and materials including stainless steel and brass.
In practical terms, the installation of Externally Threaded Inserts involves careful preparation and precise drilling. To ensure a secure fit, the substrate must be accurately drilled to the recommended diameter, followed by proper tapping if necessary. Many users find that using a countersink bit helps create a flush finish, especially when the insert is to be used in visible applications. Lubricants such as paste wax or cutting oil can be applied to ease the insertion process and protect the insert and material during installation. Detailed technical specifications provided by manufacturers should always be followed, as even a small error in drilling or tapping can compromise the performance of the insert. For more technical guidance, resources like GlobalSpec offer in-depth specifications and best practices.
Externally Threaded Inserts are also a cost-effective solution for enhancing repair and assembly processes. By eliminating the need for complete component replacement, these inserts help reduce both material waste and overall production costs. Their durability means that once installed, they rarely require maintenance, thus lowering the long-term operational expenses. In industries where budget constraints are as important as performance, such as small-scale manufacturing and DIY projects, the cost efficiency of Externally Threaded Inserts is a significant advantage. Market analyses from ThomasNet indicate that investing in quality fasteners like these can lead to substantial savings over time.
The versatility of Externally Threaded Inserts is further enhanced by their compatibility with various complementary fastening systems. They can be used in conjunction with external helicoils, threaded inserts for metal, or even nutsert systems for wood, depending on the project requirements. This interoperability ensures that designers have a wide range of options when selecting the optimal fastening solution for their needs. For example, in a repair scenario where the original threaded connection has failed, combining an external threaded sleeve with a high-strength bolt can restore the joint’s integrity without extensive rework.
Recent technological advancements have also led to improvements in the manufacturing process of Externally Threaded Inserts. Modern CNC machining and laser cutting techniques have improved the precision and consistency of these inserts, resulting in products that meet stringent quality standards. Additionally, innovative surface treatments and coatings enhance their corrosion resistance and longevity, particularly in harsh environments. Such advancements have positioned Externally Threaded Inserts as a key player in high-performance applications across various industries.
- Practical Installation Tips for Externally Threaded Inserts:
- Measure Precisely: Ensure the drill bit size matches the insert’s specifications for a secure press-fit.
- Prepare the Surface: Clean the area thoroughly to remove debris and ensure a strong bond.
- Use Appropriate Tools: Utilize a countersink bit for a flush finish and specialized insertion tools if available.
- Apply Lubricants: Use paste wax or cutting oil to facilitate smooth installation and prevent damage.
- Follow Manufacturer Guidelines: Adhere strictly to the technical specifications provided with the insert to avoid installation errors.
The performance and reliability of Externally Threaded Inserts have been validated by numerous case studies and technical evaluations. For instance, in automotive repair scenarios, replacing damaged threads with high-quality external threaded inserts has resulted in repaired joints that exceed the original strength specifications. Similarly, in woodworking and 3D printing applications, these inserts have been shown to provide robust, reusable threaded connections that withstand repeated assembly and disassembly. These real-world applications underscore the value of investing in top-tier Externally Threaded Inserts for both new projects and repairs.
As industries continue to evolve, the need for innovative fastening solutions grows. Externally Threaded Inserts offer a unique blend of performance, durability, and cost-effectiveness that is unmatched by traditional fastening methods. Their ability to provide reliable, long-lasting threaded connections makes them an essential component in modern fabrication and repair. Whether you are a professional engineer, a DIY enthusiast, or a maintenance technician, these inserts can help you achieve superior assembly results and extend the life of your components.
By choosing high-quality Externally Threaded Inserts, you are not only enhancing the structural integrity of your projects but also investing in a technology that supports efficiency and sustainability. With their proven performance in a variety of applications and ongoing advancements in manufacturing technology, these inserts are set to remain at the forefront of fastener solutions. Staying informed about the latest trends and best practices in fastener technology is essential for ensuring that your assemblies meet the highest standards of safety and reliability.
Top 10 Best Externally Threaded Inserts to Buy
- 1/4-20 threaded insert x 15mm length, 6mm allen wrench included, best 1/4″-20 threaded insert wood insert furniture scre…
- Insert head ⌀: 0.461″ / 11.7mm, body ⌀: 0.315″ / 8mm, threads ⌀: 0.410″ / 10.4mm.
- Threaded inserts are easy to install, simply drill the right size hole and Install with hex key provided.

- 40pieces Pack of 3/8-16 furniture screws threaded inserts for wood furniture such as soft woods, plywood and composition…
- Size: Internal Thread Insert Type: 3/8″-16, External Diameter: 15.35mm, Total Length: 25mm. (3/8″-16 x 25mm).
- Material: High quality carbon steel with high hardness. These furniture screws are wear-resistant and very durable to us…

- Anti-loosening: The screw threaded insert of the locking wire can lock the screw into the threaded hole, so that the scr…
- Robust: These threaded inserts have good connection performance, which can enhance connection strength and improve conne…
- Coil Type: Deep thread, not easy to slip, with certain elasticity, can make the thread force more uniform, eliminate the…

- THREADED INSERTS FOR WOOD – E-Z LOK Thread Inserts for soft wood are ideal for applications where stripping or thread er…
- PROVIDE STURDY MACHINE THREADS – E-Z Hex drive thread inserts provide sturdy machine threads in soft woods; They feature…
- FLUSH AND FLANGED DESIGNS – Zinc threaded inserts available in hex-flush threaded inserts and hex flanged threaded inser…

- THREADED INSERTS FOR METAL – E-Z LOK Thread Inserts for metal. Solid threaded inserts that are strong, easy to install, …
- INSTALL WITH STANDARD TOOLS – 303 stainless steel threaded inserts machined out of solid steel for strength. Install wit…
- QUICKLY REPAIR DAMAGED THREADS – Quickly repair damaged threads or reinforce tapped holes in soft metals with these stee…

- Easy to Use Solution For Repairing Damaged Threads in Metal
- Install With Standard Drill & Tap; NO Special Tools Needed
- Self Locking; Preapplied Adhesive Activates Upon Installation and is Fastener-Ready in 3-5 Minutes

- 1/2×28 Convert to 5/8×24
- Comes with 1 PCS Thread Protector & 1 PCS Crush Washer
- Black Oxide Finish All Steel Construction

- Easy to Use Solution For Repairing Damaged Threads in Metal
- Install With Standard Drill & Tap; NO Special Tools Needed
- Self Locking; Preapplied Adhesive Activates Upon Installation and is Fastener-Ready in 3-5 Minutes

- THREADED INSERTS FOR METAL – E-Z LOK Thread Inserts for metal. Solid threaded inserts that are strong, easy to install, …
- INSTALL WITH STANDARD TOOLS – C12L14 Carbon steel threaded inserts. Install with standard tools. No special drills, taps…
- QUICKLY REPAIR DAMAGED THREADS – Quickly repair damaged threads or reinforce tapped holes in soft metals with these stee…

- THREADED INSERTS FOR METAL – E-Z LOK Thread Inserts for metal. Solid threaded inserts that are strong, easy to install, …
- INSTALL WITH STANDARD TOOLS – 12L14 Carbon steel threaded inserts. Install with standard tools. No special drills, taps,…
- QUICKLY REPAIR DAMAGED THREADS – Quickly repair damaged threads or reinforce tapped holes in soft metals with these stee…

Expert Analysis and Practical Recommendations on Externally Threaded Inserts
In the latter segment of our discussion, we delve into expert insights and practical recommendations for optimizing the use of Externally Threaded Inserts. Field tests and comparative studies consistently show that these fasteners provide excellent torque resistance and pull-out strength when installed correctly. Their external threading design, which includes variations such as external helicoils and threaded inserts for metal, offers a robust and adaptable solution for a multitude of applications.
One critical factor in achieving optimal performance with Externally Threaded Inserts is precise measurement and installation. It is imperative to follow manufacturer guidelines for drilling and tapping to ensure a perfect press-fit. Professionals recommend using digital torque wrenches and calibrated insertion tools to minimize errors during installation. Additionally, regular inspection of the installed inserts for signs of wear or loosening is vital to maintaining long-term reliability. Technical specifications available on GlobalSpec and ThomasNet provide valuable benchmarks for torque-out and pull-out resistance, ensuring that your installation meets rigorous standards.
Material selection is also key when working with Externally Threaded Inserts. For applications in corrosive environments, stainless steel variants are highly recommended for their superior resistance to rust and degradation. Brass and other alloy options may be preferred in decorative or less demanding applications due to their aesthetic qualities and cost-effectiveness. The choice between different types of external threaded bushings and sleeves often comes down to the specific load and environmental conditions of your project. By comparing products from various manufacturers and reading customer reviews, you can select the most suitable insert for your needs.
The versatility of Externally Threaded Inserts makes them indispensable for both new construction and repair projects. They are commonly used in automotive assembly, metal fabrication, and even high-precision 3D printed components, where a secure, reusable thread is essential. Many fabricators have noted that integrating these inserts into their assembly process has significantly reduced downtime and improved the overall strength of their joints. This performance advantage not only enhances product reliability but also contributes to reduced maintenance costs and increased operational efficiency.
For those looking to maximize the benefits of Externally Threaded Inserts, here are some expert recommendations:
- Ensure Accurate Drilling: Use the correct drill bit size as specified by the manufacturer to achieve a precise fit.
- Utilize Countersinking: A countersink bit can help achieve a flush finish, especially in applications where aesthetics are critical.
- Select the Right Material: Choose stainless steel for harsh environments and brass for decorative purposes.
- Apply Lubrication: Use paste wax or cutting oil to facilitate smooth insertion and reduce the risk of damage.
- Adhere to Technical Guidelines: Follow detailed installation procedures provided in the product datasheet for optimal performance.
Advancements in fastener technology have further refined the design of Externally Threaded Inserts. Modern manufacturing techniques, including CNC machining and laser cutting, have resulted in products with highly accurate thread profiles and improved surface finishes. These enhancements contribute to the overall performance and durability of the inserts, making them an ideal solution for a wide range of industrial applications. Continuous improvements in design and materials ensure that Externally Threaded Inserts remain at the cutting edge of fastener technology.
User testimonials and independent testing have consistently demonstrated the reliability and strength of Externally Threaded Inserts. For example, in one series of tests conducted by industry experts, these inserts provided superior torque resistance and were less likely to strip compared to traditional thread repair methods. This performance is critical in applications where safety and long-term durability are non-negotiable, such as in aerospace and heavy machinery. The robust performance of these inserts, as confirmed by sources like GlobalSpec, highlights their value in modern fabrication processes.
By choosing high-quality Externally Threaded Inserts, you invest in a fastener solution that enhances both the functionality and longevity of your projects. Their ease of installation, combined with superior mechanical properties, makes them a smart choice for professionals and DIY enthusiasts alike. As the fastener market continues to evolve, staying updated with the latest innovations in Externally Threaded Inserts will ensure that your assemblies are both secure and efficient.
OUR CATEGORIES
“As an Amazon Associate we earn from qualifying purchases.”