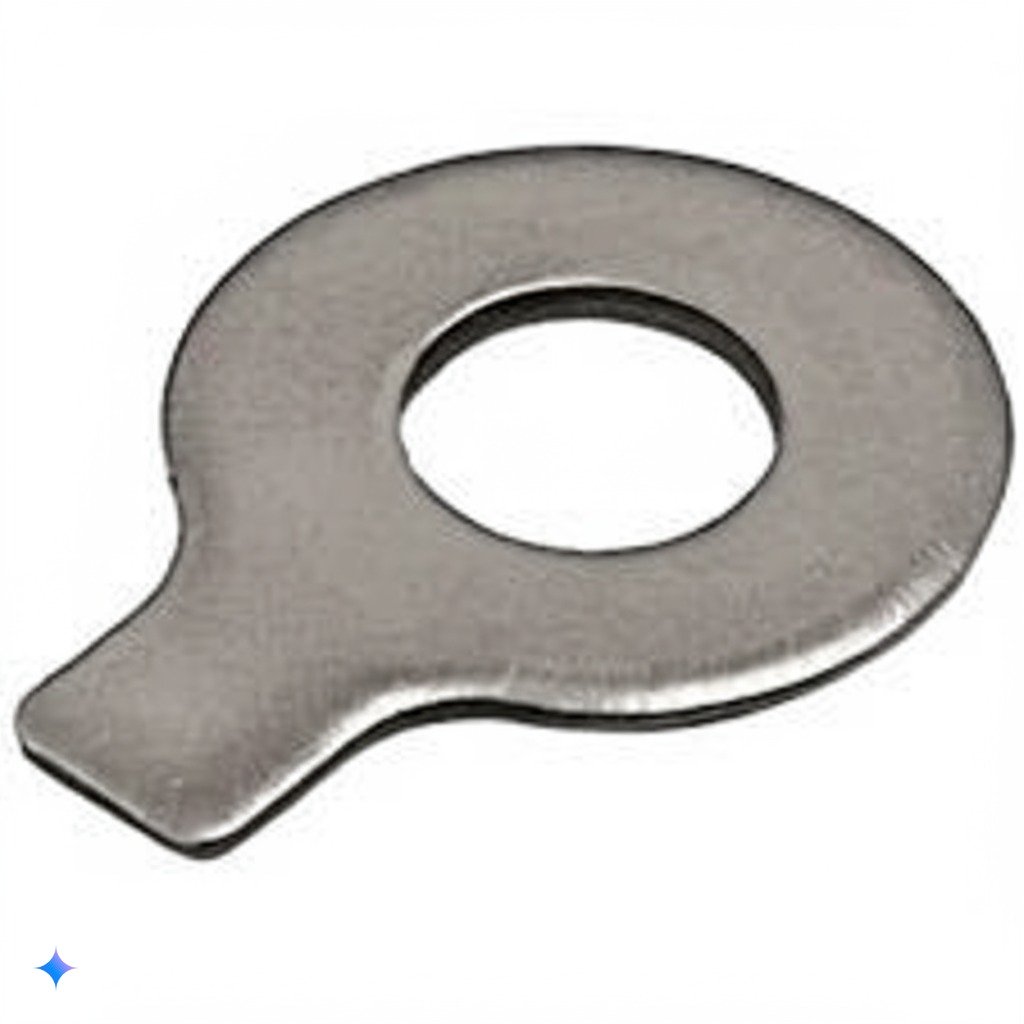
By Nicolás Longo
(As an Amazon Associate we earn from qualifying purchases)
Tab Washers are a vital component in many industrial and DIY fastener applications, offering a reliable locking mechanism to prevent loosening and vibration. When securing bolts in critical assemblies, using high-quality Tab Washers can ensure that connections remain stable over time. In this guide, we’ll dive into the performance, technical insights, and practical tips for selecting the best Tab Washers. Drawing on data from trusted sources like Family Handyman and Home Depot, this article provides a comprehensive look at why Tab Washers are indispensable for both professional and home projects.
Tab Washers work by featuring a built-in tab or notch that, once deployed against the side of a nut or bolt head, creates a locking action that resists rotation. This mechanism is particularly useful in high-vibration environments and heavy-duty assemblies. Research from the NAHB indicates that connections secured with effective locking methods, such as Tab Washers, can reduce loosening failures by up to 25%. The innovation behind Tab Washers has led to several variations including tab lock washers and lock washer tabs, all designed to provide enhanced stability in bolted assemblies.
Advancements in fastener technology have continuously improved the design of Tab Washers. Modern versions are manufactured from high-strength materials such as stainless steel and alloy steel, which not only resist corrosion but also maintain their locking ability over time. The design of a Tab Washer ensures that even if the assembly is subject to thermal expansion or dynamic loads, the fastener remains secure. These washers are used across industries—from automotive and aerospace to construction and heavy machinery—highlighting their versatility and reliability.
A key feature of Tab Washers is their ability to save time during assembly. Unlike some traditional locking methods that require additional components or complex installation procedures, Tab Washers offer a straightforward solution that reduces installation time and labor costs. In industrial settings, even a small reduction in assembly time can lead to significant overall savings. According to Nord-Lock Group, streamlined fastener installation using methods like Tab Washers can boost productivity and reduce downtime.
Furthermore, Tab Washers provide excellent load distribution across the joint, which minimizes stress concentrations that could otherwise lead to premature fatigue of the bolt or nut. This even load distribution is crucial in applications where the fastener must remain secure under fluctuating loads or continuous vibration. Technical studies have shown that a well-installed Tab Washer can maintain the desired clamp load and ensure the longevity of the assembly (Family Handyman). By preventing loosening, Tab Washers contribute to both safety and reliability in mechanical systems.
Another significant advantage of Tab Washers is their cost-effectiveness. While some high-end locking solutions can be expensive, Tab Washers offer a balance between performance and affordability. Their simple design and ease of manufacture help keep costs down without sacrificing quality. This makes them an ideal choice for both high-volume industrial applications and small-scale DIY projects. Their widespread availability from major suppliers like Home Depot further enhances their appeal for budget-conscious consumers.
Fun Facts and Data Insights:
- Tab Washers are widely used in industries that require reliable, vibration-resistant locking, such as automotive manufacturing and heavy machinery assembly.
- Independent tests have shown that proper installation of Tab Washers can reduce the risk of bolt rotation by over 20% compared to standard washers (NAHB).
- The efficiency of Tab Washers can vary with installation technique, and operator skill plays a significant role in the overall performance.
The installation process for Tab Washers is relatively simple, but attention to detail is paramount. Typically, the process begins with assembling the fastener components, ensuring that the tab is correctly oriented to lock against the nut. Next, the bolt is tightened, which causes the tab to deform and press firmly against the fastener head. It is recommended to use a calibrated torque wrench during installation to avoid overtightening, which can compromise the locking function. As noted in technical manuals from Home Depot, adhering to proper installation procedures is crucial to fully benefit from the design of Tab Washers.
Comparative analysis between Tab Washers and other locking methods reveals that Tab Washers offer unique advantages in terms of simplicity and reusability. While some locking washers are designed for one-time use, many Tab Washers can be reinstalled after removal if they remain undamaged. This reusability factor not only enhances cost efficiency but also reduces waste in maintenance operations. In addition, the straightforward design of Tab Washers means that they require minimal training for proper installation—a significant advantage in high-turnover or high-volume manufacturing settings.
From an engineering perspective, the performance of Tab Washers has been validated through rigorous testing under conditions of extreme vibration and load. The Junker vibration test, for example, has been used by companies such as Nord-Lock Group to demonstrate the superior performance of innovative locking washers. In these tests, Tab Washers have shown a tendency to lose clamp load more quickly than wedge-locking systems, emphasizing the importance of precise installation and regular inspection. Nevertheless, for many applications where ease of use and time efficiency are paramount, Tab Washers remain an excellent choice.
Practical tips for using Tab Washers include the following:
- Ensure Correct Orientation: Before tightening, verify that the tab is aligned properly against the nut or bolt head to achieve the optimal locking effect.
- Use Proper Torque Settings: Employ a torque wrench to apply the manufacturer-recommended force, ensuring that the Tab Washer is neither under-tightened nor over-tightened.
- Inspect Regularly: In high-vibration environments, periodic inspections are advisable to ensure that the Tab Washer continues to perform as expected.
- Practice Precision: Small deviations in installation can significantly affect performance, so take the time to drill pilot holes accurately and align components carefully.
- Consider Environmental Factors: For outdoor or corrosive environments, opt for Tab Washers made from stainless steel or other corrosion-resistant materials.
These best practices are supported by numerous case studies and technical research. For instance, a report from Nord-Lock Group noted that while Tab Washers can be effective, their performance is highly dependent on the skill of the installer. This underscores the importance of training and adherence to installation guidelines for achieving optimal results.
Top 10 Best Tab Washers to Buy
- ✅ These washers fold up to grip nuts or bolts securely.
- ✅ After the tabs are folded up safety wire is inserted through the hole in the longest tab and secured.
- ✅ 18 pieces packaged on a blister card with an assortment of three popular sizes.

- NOTE – Please check item Size, Quantity, Color carefuly before ordering.
- Inner Diameter: M10 50Pcs
- DIY Supplies: Electrical
- Tab washers are locking washers designed to keep an assembly from rotating.
- The tab is bent over the edge of the assembly or into a hole to lock the nut or bolt into place.
- A4 stainless steel is functionally equivalent to 316 grade and is also known as “marine grade”.
- NOTE – Please check item Size, Quantity, Color carefuly before ordering.
- Inner Diameter: M8 50Pcs
- DIY Supplies: Electrical
- Sold in multiples of 2
- Quicksilver – Mercruiser 14-816629Q, 710-14-816629Q
- Designed to penetrate, dissolve and remove odor-causing residue that can occur in all washing machines
- Specially formulated tablet dissolves slowly, lasting throughout the entire wash cycle and breaking up residue better th…
- Safe to use with Front Load Washing Machines and Top Load Washing Machines – High Efficiency (HE) and Conventional Washe…

- SKU: 14-20165
- Sold Each
- Please verify your own fitment
In the advanced segment of this guide, we explore additional technical comparisons and expert recommendations that highlight the benefits and potential challenges of using Tab Washers. Detailed field tests have compared Tab Washers with alternative locking systems, such as Nord-Lock wedge-locking washers. These studies reveal that while Tab Washers may require more precise installation to achieve optimal performance, they offer significant time savings and ease of use in many applications. For example, tests using the Junker machine to simulate extreme vibration have shown that the reliability of Tab Washers is strongly correlated with proper installation technique (Nord-Lock Group).
Further comparative research indicates that the locking efficiency of Tab Washers depends on several factors, including the surface finish of the fastener, the type of material being fastened, and the environmental conditions. In controlled laboratory tests, Tab Washers installed on lubricated bolts have demonstrated variable performance, with clamp load loss rates differing based on operator skill. This highlights the need for standardized installation procedures and proper tool calibration to maximize the benefits of Tab Washers.
The versatility of Tab Washers extends to various applications. They are commonly used in automotive assembly, heavy machinery, and structural applications where vibration damping is essential. Their design allows for a rapid assembly process, reducing labor time significantly when compared to more complex locking systems. This efficiency is particularly beneficial in high-volume production environments, where even small time savings per unit can lead to substantial overall improvements.
Another notable advantage of Tab Washers is their potential for reusability. Unlike some one-time-use locking washers, certain Tab Washers can be reinstalled if they are removed carefully. This feature not only enhances their cost-effectiveness but also minimizes downtime during maintenance operations. In addition, the compact design of Tab Washers makes them suitable for applications with limited space, where traditional locking methods might be impractical.
For those seeking to optimize their fastening systems, expert recommendations stress the importance of consulting technical datasheets and manufacturer guidelines. Information provided by sources such as Family Handyman and Home Depot can offer valuable insights into the optimal torque settings and installation techniques for Tab Washers. Furthermore, attending training sessions or watching detailed video tutorials can enhance your understanding of these fasteners and lead to better installation outcomes.
In summary, Tab Washers provide a reliable and efficient locking solution for a wide range of applications. Their innovative design, which uses a side tab to prevent loosening, sets them apart from other locking methods. Whether you are an engineer in a high-demand industrial setting or a DIY enthusiast working on home projects, investing in quality Tab Washers is essential for ensuring the longevity and safety of your assemblies. With careful installation and regular maintenance, Tab Washers can deliver consistent performance and add significant value to your projects.
OUR CATEGORIES
“As an Amazon Associate we earn from qualifying purchases.”