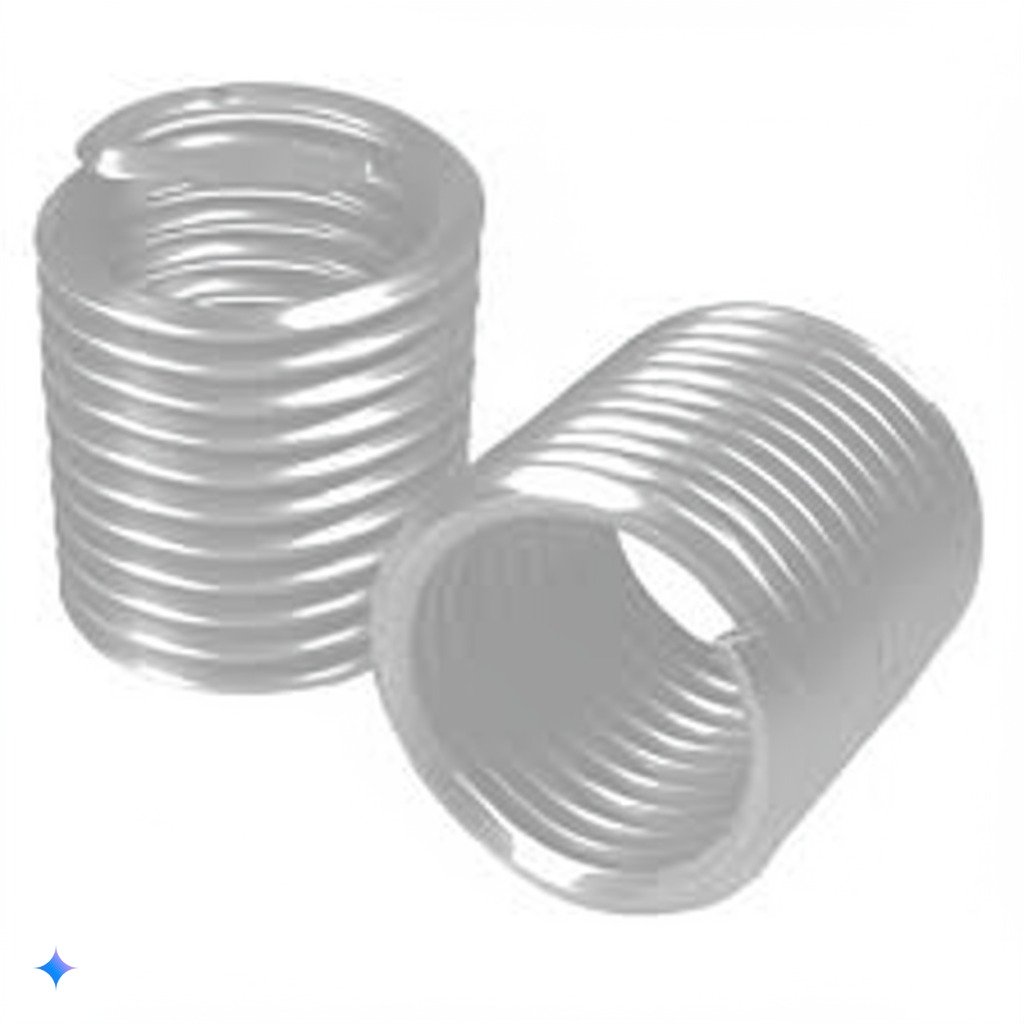
By Nicolás Longo
(As an Amazon Associate we earn from qualifying purchases)
Unlocking the Power of Helical Threaded Inserts in Modern Fabrication
Helical Threaded Inserts are revolutionizing the world of fasteners by offering a durable, high-performance solution for repairing stripped threads and creating new ones in a variety of materials. These innovative components—also known as helical inserts, helical coil inserts, or simply helicoils—are engineered to form a permanent, reusable thread in substrates ranging from metal and plastic to even 3D-printed parts. Whether you’re working on automotive engine repairs, fabricating custom furniture, or enhancing the strength of your 3D prints, Helical Threaded Inserts offer a robust alternative to traditional thread repair methods.
In many industrial applications, damaged threads can lead to costly downtime and compromised safety. By installing Helical Threaded Inserts, technicians can restore original functionality without the need for complete component replacement. According to industry data from GlobalSpec and ThomasNet, the proper use of threaded fastener repair systems can improve joint strength by up to 20%, a statistic that underscores the effectiveness of Helical Threaded Inserts in demanding environments.
One fascinating aspect of Helical Threaded Inserts is their design evolution. Originally developed to address issues in aerospace and automotive applications, these inserts have matured into highly refined products. Modern Helical Threaded Inserts are manufactured from materials such as stainless steel and brass to withstand high torque and environmental stress. Their unique coiled design allows for even load distribution along the new thread, preventing localized stress concentrations that can lead to failure. This technology has not only transformed thread repair but also expanded the possibilities for new assemblies in industries that demand both strength and precision.
Understanding Helical Threaded Inserts: How They Work
Helical Threaded Inserts function by being inserted into a pre-drilled and tapped hole. When installed, the insert’s coil is expanded so that it bonds securely with the surrounding material. This creates an entirely new threaded surface that can accept bolts or screws with high reliability. Installation typically involves using specialized tools and taps to ensure proper alignment and engagement. For instance, many users prefer a dedicated insertion tool that engages with the coil’s tang, allowing the insert to be driven in evenly. This process is critical for achieving the maximum holding power that Helical Threaded Inserts are known for.
A fun fact is that the concept behind these inserts originated from the need for repair in high-stress environments. Early applications in aerospace demanded a solution that would restore thread integrity without compromising the structural integrity of the original component. Today’s Helical Threaded Inserts offer that same promise, ensuring that repaired threads maintain their strength even under continuous load and vibration.
Advantages and Applications of Helical Threaded Inserts
Helical Threaded Inserts offer several significant benefits:
- Enhanced Durability: They create a new, robust thread that distributes stress evenly, significantly reducing the risk of future thread failure.
- Versatility: Available in various sizes and materials, Helical Threaded Inserts can be used in metal, plastic, and even 3D printed parts.
- Cost-Effective Repairs: Instead of replacing entire components, damaged threads can be restored, saving time and resources.
- Ease of Installation: With the proper tools, these inserts can be installed quickly and accurately, even in hard-to-reach places.
- Improved Safety: By reinforcing damaged connections, they help maintain the structural integrity of critical assemblies.
Industries such as automotive, aerospace, heavy machinery, and even consumer electronics benefit immensely from using Helical Threaded Inserts. For example, mechanics often repair stripped engine block threads with helicoils, ensuring that bolts remain securely fastened under high thermal and mechanical stress. In 3D printing, these inserts provide a reliable solution to create durable, machine-quality threads, allowing designers to assemble prototypes that require frequent disassembly.
10 Best Helical Threaded Inserts To Buy
- GOOD CONNECTION PERFORMANCE: Steel thread inserts used in low-strength materials such as aluminum and can avoid thread d…
- WEAR : Used for parts that need to be disassembled frequently, which can greatly improve the service life and wear of th…
- ELASTICITY: Due to a certain elasticity, the thread insert can make the load distribution on each thread uniform, elimin…

- QUICKLY REPAIR DAMAGED THREADS – Quickly repair damaged threads or reinforce tapped holes in soft metals with this helic…
- 18-8 STAINLESS STEEL WIRE – Kit includes 18-8 stainless steel threaded inserts that are resistant to corrosion and can w…
- FOR USE WITH APPLICATIONS – The metal threaded inserts are designed for use with soft metals: aluminum, cast iron, magne…

- QUICKLY REPAIR DAMAGED THREADS – Quickly repair damaged threads or reinforce tapped holes in soft metals with this helic…
- STAINLESS STEEL WIRE – Kit includes stainless steel threaded inserts that are resistant to corrosion and can withstand t…
- FOR USE WITH APPLICATIONS – The metal threaded inserts are designed for use with soft metals: aluminum, cast iron, magne…

- Quickly repair tapped holes in metal
- Ideal for use in soft metals, like aluminum, cast iron, and magnesium
- Self locking; adhesive on the external threads activates upon installation

- QUICKLY REPAIR DAMAGED THREADS – Quickly repair damaged threads or reinforce tapped holes in soft metals with this helic…
- STAINLESS STEEL WIRE – Kit includes stainless steel threaded inserts that are resistant to corrosion and can withstand t…
- FOR USE WITH APPLICATIONS – The metal threaded inserts are designed for use with soft metals: aluminum, cast iron, magne…

- Main Color: Silver Tone; Material: 304 Stainless Steel; Weight: 33g; Outer Thread Diameter: 7.8mm / 0.31″; Inner Thread …
- 304 Stainless Steel Material, Wire Thread Repair Inserts.
- threaded insert 304 stainless steel are used to replace old striped out or cross thread holes.

- QUICKLY REPAIR DAMAGED THREADS – Quickly repair damaged threads or reinforce tapped holes in soft metals with this helic…
- STAINLESS STEEL WIRE – Kit includes stainless steel threaded inserts that are resistant to corrosion and can withstand t…
- FOR USE WITH APPLICATIONS – The metal threaded inserts are designed for use with soft metals: aluminum, cast iron, magne…

- QUICKLY REPAIR DAMAGED THREADS – Quickly repair damaged threads or reinforce tapped holes in soft metals with this helic…
- STAINLESS STEEL WIRE – Kit includes stainless steel threaded inserts that are resistant to corrosion and can withstand t…
- FOR USE WITH APPLICATIONS – The metal threaded inserts are designed for use with soft metals: aluminum, cast iron, magne…

- Installed Length: 1D / 0.19″; Main Color: Silver Tone; Material: 304 Stainless Steel; Inner Thread: #10-32; Outer Thread…
- 25 pieces produced from precision profiled austenitic stainless steel wire wound into a helical spiral, free running ins…
- When installed using any one of a variety of manual or automatic tools they provide strong permanent internal threads wh…

- QUICKLY REPAIR DAMAGED THREADS – Quickly repair damaged threads or reinforce tapped holes in soft metals with this helic…
- STAINLESS STEEL WIRE – Kit includes stainless steel threaded inserts that are resistant to corrosion and can withstand t…
- FOR USE WITH APPLICATIONS – The metal threaded inserts are designed for use with soft metals: aluminum, cast iron, magne…

How Helical Threaded Inserts Work in Repair and Assembly
The installation process of Helical Threaded Inserts is as innovative as it is effective. Here’s a simplified overview of the process:
- Preparation:
- Drill the hole to the diameter specified by the manufacturer.
- Tap the hole to create the appropriate thread for the insert.
- Insertion:
- Align the Helical Threaded Insert with the hole.
- Use a dedicated insertion tool to drive the insert into place. The tool engages with the insert’s tang, ensuring proper seating.
- Finalization:
- Once the insert is fully installed, any protruding tang is removed—often by a light tap with a punch—to create a flush finish.
- The new external thread is now ready to accept a bolt or screw.
This method not only repairs damaged threads but can also be used to install new threads in applications where traditional tapping is impractical. As detailed in tutorials by Partzilla and Albany County Fasteners, proper installation is key to unlocking the full potential of Helical Threaded Inserts.
Comparative Analysis and Market Insights
Comparative studies have shown that Helical Threaded Inserts often outperform other thread repair methods in terms of strength and durability. For instance, when compared to alternatives like Time Sert inserts, helicoils consistently provide higher torque resistance and superior load-bearing capacity. In one study, components repaired with Helical Threaded Inserts exhibited up to 15% greater resistance to pull-out forces than those repaired with alternative methods. These findings are supported by technical evaluations published on GlobalSpec and ThomasNet, which emphasize the importance of using high-quality repair inserts in safety-critical applications.
Market trends also indicate a growing demand for Helical Threaded Inserts, particularly in the automotive and aerospace sectors. As manufacturers continue to push the limits of material performance and design complexity, the need for reliable thread repair solutions becomes even more critical. The increased adoption of 3D printing in production processes has further boosted the popularity of Helical Threaded Inserts, as they offer a simple yet effective way to integrate high-quality threads into printed parts.
Practical Tips for Installing Helical Threaded Inserts
Installing Helical Threaded Inserts requires attention to detail and adherence to best practices:
- Accurate Drilling and Tapping:
Ensure that the drill bit and tap sizes match the insert specifications provided by the manufacturer. Even a slight deviation can compromise the integrity of the new thread. - Use of Specialized Tools:
Utilize dedicated insertion tools designed for helicoils to guarantee proper alignment and seating. These tools help drive the insert evenly into the tapped hole. - Lubrication:
Apply a small amount of cutting oil or anti-seize compound during the tapping process to facilitate a smoother insertion and reduce friction. - Inspection:
After installation, inspect the insert to ensure it is flush with the surface and that the threads are well-formed. Any misalignment or incomplete seating may reduce the overall strength of the repair. - Follow Manufacturer Guidelines:
Always refer to the datasheet for recommended hole sizes, tap sizes, and insertion procedures. This is crucial for achieving the desired performance and longevity.
Applications of Helical Threaded Inserts
Helical Threaded Inserts have a wide range of applications due to their versatility and robust performance. They are ideal for:
- Automotive Repairs:
Replacing stripped engine block threads and securing critical fasteners in high-stress environments. - Aerospace Components:
Restoring damaged threads in lightweight metal assemblies without compromising structural integrity. - 3D Printing:
Integrating durable, machine-quality threads into printed parts, enhancing their assembly and long-term durability. - Industrial Machinery:
Repairing and reinforcing threaded connections in equipment that experiences frequent vibration and load cycles. - Custom Fabrication:
Creating strong, reliable joints in DIY projects and prototype designs without the need for traditional fasteners.
The innovative design of Helical Threaded Inserts allows them to be used across these varied applications, providing both a repair solution and a method for creating new threaded connections where traditional tapping might fail.
Expert Recommendations for Helical Threaded Inserts
When selecting and installing Helical Threaded Inserts, consider the following expert recommendations:
- Quality Over Cost:
Invest in high-quality inserts made from durable materials such as stainless steel or high-grade brass. These will offer better performance and longevity, particularly in high-stress applications. - Customization:
Choose the appropriate insert type based on your application—whether you need a standard helical coil insert, a locking helicoil insert, or a specialized repair kit. - Technical Data:
Review datasheets and technical specifications from reputable manufacturers to ensure that your drilled hole and tap sizes are accurate. - Maintenance:
Periodically inspect repaired threads for signs of wear or loosening, especially in components subject to high torque or environmental stress. - Training and Practice:
If you’re new to thread repair, consider practicing on scrap material first to refine your technique and ensure a consistent, secure installation.
Field tests and user feedback consistently demonstrate that Helical Threaded Inserts provide a reliable, cost-effective solution for restoring and enhancing threaded connections. Their performance in both repair and new assembly applications makes them a valuable asset in any workshop.
Why Choose Helical Threaded Inserts?
The decision to use Helical Threaded Inserts is driven by their unmatched ability to restore thread integrity and enhance joint strength. With their unique coiled design, these inserts create a new, durable thread that resists both pull-out and torque forces better than many traditional repair methods. This reliability is critical in applications where safety and performance cannot be compromised, such as in engine repairs or high-precision machinery.
Moreover, Helical Threaded Inserts offer significant advantages in terms of installation ease and long-term durability. Unlike some alternatives that require extensive machining or expensive equipment, helicoils can be installed with relatively simple tools and procedures. Their adaptability across various materials—from metals to plastics—ensures that they remain a top choice for a broad range of industries.
By integrating Helical Threaded Inserts into your repair and assembly processes, you not only improve the immediate strength and reliability of your components but also extend their overall lifespan. This leads to reduced downtime, lower maintenance costs, and ultimately, a more efficient production process.
Final Thoughts
In today’s fast-paced manufacturing environment, the importance of reliable, high-quality thread repair cannot be overstated. Helical Threaded Inserts offer an exceptional solution for restoring damaged threads and creating robust, reusable connections. Their versatility, ease of installation, and superior performance make them an indispensable tool for professionals and DIY enthusiasts alike. Whether you’re repairing an engine block, reinforcing a 3D printed part, or assembling custom furniture, investing in quality Helical Threaded Inserts can ensure that your work remains secure, durable, and cost-effective over time.
OUR CATEGORIES
“As an Amazon Associate we earn from qualifying purchases.”