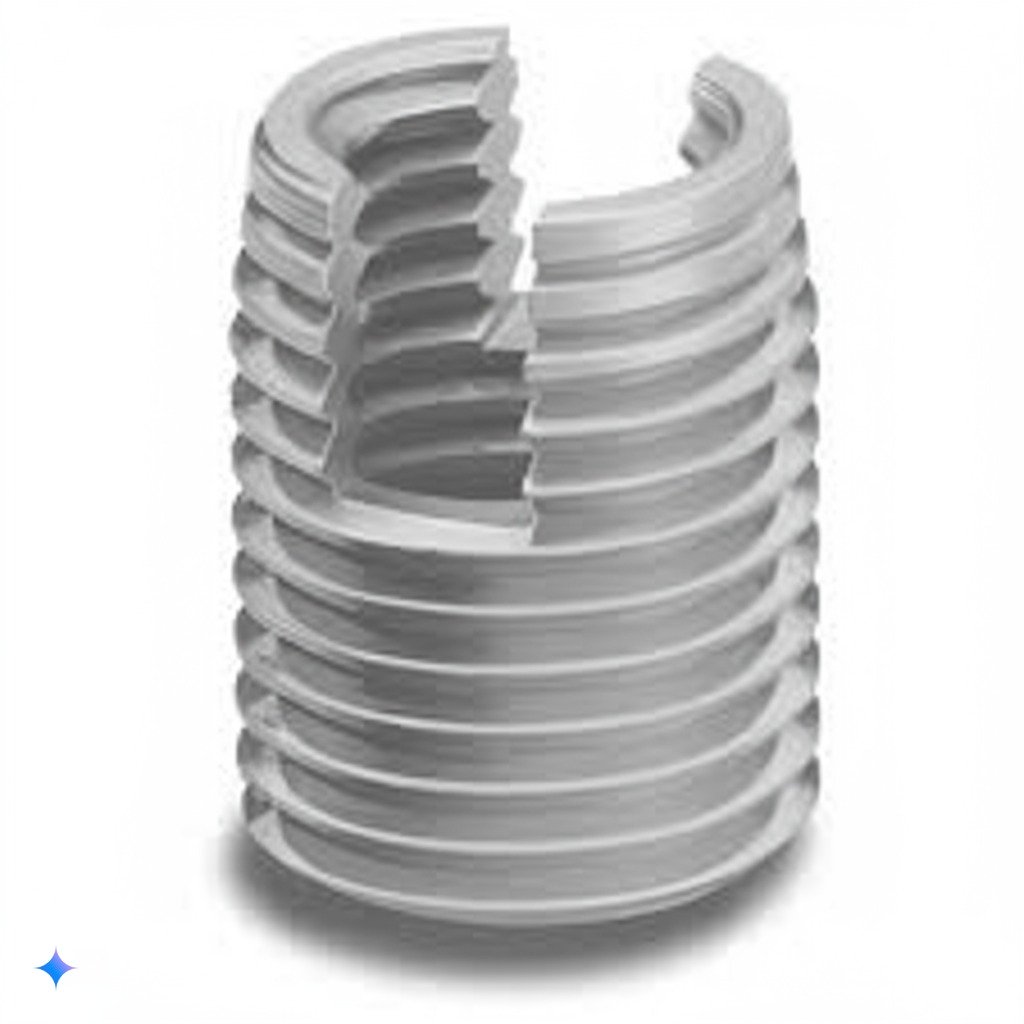
By Nicolás Longo
(As an Amazon Associate we earn from qualifying purchases)
Revolutionize Your Fastening Projects with Tapping Inserts
Tapping Inserts are essential fasteners for repairing or reinforcing threads in a variety of applications. These innovative components provide a secure, durable interface for machine screws in metals, plastics, and even composites. When used correctly, tapping inserts can restore stripped threads or strengthen connections in critical assemblies, saving time and cost compared to complete part replacement. Modern tapping inserts are engineered for high torque and pull-out resistance, making them ideal for automotive, aerospace, and industrial applications. They come in diverse materials such as stainless steel, brass, and carbon steel, each tailored to specific load and environmental conditions. With advancements in design and manufacturing, tapping inserts have become a go-to solution for both professional fabricators and DIY enthusiasts.
The beauty of tapping inserts lies in their ability to convert damaged or soft threaded holes into robust, reusable connections. They are often installed by tapping a new thread into a pre-drilled hole and then pressing the insert in place. This method not only repairs the original thread but also provides a precise, standardized interface that accepts bolts or screws with ease. Recent studies in fastener technology have shown that using tapping inserts can increase thread strength by up to 20% compared to conventional repair methods (Acme Industrial Co., 2013). The process is both efficient and cost-effective, which explains why tapping inserts continue to gain popularity in modern manufacturing environments.
Moreover, tapping inserts have evolved to address the challenges posed by new materials and manufacturing techniques, including 3D printing and composite molding. For example, tapping insert kits now come with detailed datasheets specifying the recommended drill size, thread pitch, and insertion depth to ensure maximum performance. This attention to detail is crucial because even a slight deviation in hole dimensions can compromise the holding strength of the insert. In practice, fabricators rely on tapping inserts to maintain quality in assemblies where precision and reliability are paramount. Their versatility also allows them to be used in repair work on engines, structural components, and consumer products, reinforcing their role as a vital fastener solution.
When selecting tapping inserts, it is important to consider the material of the parent part, the expected load, and the installation method. For softer metals or plastics, inserts with a flanged design can distribute stress more evenly, reducing the risk of damage to the surrounding material. In high-torque applications, high-grade stainless steel tapping inserts are preferred for their exceptional durability and corrosion resistance. Additionally, tapping inserts designed for composite materials offer unique benefits, such as improved resistance to creep and fatigue. These variations ensure that tapping inserts remain adaptable to the evolving demands of modern manufacturing and repair tasks.
A significant advantage of tapping inserts is their ease of installation. Unlike welding or complete thread replacement, tapping inserts require only standard drilling and tapping tools, which are readily available in most workshops. The process is straightforward: drill a pilot hole to the precise dimensions recommended by the manufacturer, tap the hole to create a new thread profile, and then press in the tapping insert until it is flush with the surface. This simplicity translates into faster assembly times and less risk of damage during installation. Whether you’re a seasoned professional or a hobbyist, the installation of tapping inserts is an accessible skill that can greatly improve your repair and assembly processes.
In addition to their functional benefits, tapping inserts offer economic advantages. By restoring the integrity of damaged threads, they eliminate the need for expensive part replacements. This not only reduces material costs but also minimizes downtime in production environments. Industries that depend on high uptime, such as aerospace and automotive, have reported significant savings by incorporating tapping inserts into their maintenance protocols. Furthermore, the modular nature of tapping insert systems means that they can be easily replaced or upgraded, ensuring that your assembly remains state-of-the-art without requiring a complete overhaul.
Another compelling reason to choose tapping inserts is the environmental benefit. By extending the lifespan of components and reducing waste from failed fasteners, tapping inserts contribute to more sustainable manufacturing practices. In a world where efficiency and sustainability are increasingly important, tapping inserts provide a solution that aligns with both performance and environmental goals. Their reusability and ease of replacement mean that less scrap material is generated, making them an eco-friendly option for many applications.
Top 10 Best Tapping Inserts to Buy
- Threaded inserts are made of high quality stainless steel ,anti- and rust, good toughness, high hardness and low abrasio…
- With certain elasticity and even load,metric thread inserts are resistant to vibration to avoid loosening.
- Tapping Inserts can be used repeatedly, can also repair the damaged thread by installing into thread hole.
- Tap- Installation: Say goodbye to time-consuming and costly tapping processes with the self-tapping insert. It eliminate…
- Enhanced Thread Strength: These self-tapping inserts provide a larger area with the finished product, resulting in stron…
- Vibration Resistance: With their unique design, these inserts offer strong to vibration, preventing loosening and guaran…

- 【Easy to Install】These self-tapping thread inserts has self-tapping ability, does not need to be pre-tapped, can be dire…
- 【Sturdy & Wear-resistance】These threaded inserts have a good connection performance, can enhance connection strength and…
- 【You Can Get】Silver, total 50Pcs. 10 x M3*0.5-M5*0.5 L6, 10 x M4*0.7-M6.5*0.75 L8, 10 x M5*0.8-M8*1.0 L10, 5 x M6*1.0-M1…

- Durable and Wear-resistant: These threaded inserts have good connection performance, which can improve connection streng…
- Total 50Pcs: 10 x M3*0.0.5-5-M5 5-M5 5*0.5 5 L6, 10 x M3*0.5 5-5-M5 5 5 L6, 10 x M6 6.5 5-5-M6.5 5-5 5 5 5-M6.5 5-M8*0.8…
- Help Maintain: Solid texture, not easy to move, deep thread, uniform force, no burrs on the thread, clear and neat. Afte…

- 【Easy to Install】These self-tapping thread inserts has self-tapping ability, does not need to be pre-tapped, can be dire…
- 【Sturdy & Wear-resistance】These threaded inserts have a good connection performance, can enhance connection strength and…
- 【You Can Get】Silver, total 50Pcs. 10 x M3*0.5-M5*0.5 L6, 10 x M4*0.7-M6.5*0.75 L8, 10 x M5*0.8-M8*1.0 L10, 5 x M6*1.0-M1…

- 【Easy To Use】 The self tapping screw sleeve does not need to be tapped in advance, and can be directly screwed into the …
- 【Easy To Maintenance】 Easy to maintenance, install a thread insert into a damage screw hole, then the screw hole can be …
- 【Excellent Performance】 The self tapping screw sleeve can solve the problem of thread crushing and effectively improve t…

- Efficient Thread Repair Tool – This kit contains 10 threaded inserts with internal M4 x 0.7mm and external M6 x 1mm thre…
- 303 Stainless Steel Material – Made from durable 303 stainless steel, these thread inserts are built to withstand the te…
- Exquisite Workmanship – Each reducing nut in this set is carefully crafted with clear threads and strong practicality. T…

- HIGH QUALITY: Made of high quality stainless steel, it is of high hardness and low abrasion.
- FEATURE: With certain elasticity and even load, it is resistant to vibration to avoid loosening. Greatly improve strengt…
- GOOD CHARACTER: Solid, is not easy to slick, deep thread, uniform force, no burr in thread, clear and tidy.

- Made of high quality stainless steel, it is of high hardness and low abrasion.
- Greatly improve strength and stability of screws connection.
- With certain elasticity and even load, it is to vibration to avoid loosening.

- main function: self tapping threaded insert is of fastener that enhance the thread strength. when embedded in soft mater…
- unthreaded heat insert, improve the strength and stability of the screw connection.
- easy to use: easy and quick to install with one assembly tool.

Expert Insights and Final Recommendations on Tapping Inserts
In wrapping up our exploration of tapping inserts, it is clear that these fasteners are indispensable for anyone involved in thread repair or high-stress assembly work. Experts agree that tapping inserts provide superior strength and durability compared to other repair methods, particularly in applications where safety and reliability are critical. According to Acme Industrial Co., proper use of tapping inserts can enhance load-bearing capacity by up to 20%, making them an excellent choice for heavy-duty applications.
For optimal performance, it is crucial to follow manufacturer guidelines for hole size, tapping depth, and installation pressure. Utilizing a calibrated drill press and quality cutting tools can ensure that the new threads are accurately formed and that the tapping insert is securely seated. Additionally, some professionals recommend the use of lubricant during the tapping process to reduce friction and heat, which helps maintain the integrity of both the insert and the surrounding material.
A comparative analysis of various tapping insert kits reveals that those made from stainless steel and brass tend to offer the best performance in corrosive environments. In contrast, carbon steel tapping inserts are typically used for repair work where cost is a more significant factor. When choosing a tapping insert, consider not only the material but also the specific design features, such as whether the insert includes a flanged head for better load distribution or a keyed locking mechanism for added security.
Real-world applications of tapping inserts demonstrate their versatility. In automotive repairs, tapping inserts have been used to restore stripped threads on engine blocks, while in the aerospace industry, they ensure that components withstand extreme vibrations and thermal stresses. Moreover, tapping inserts are now a staple in 3D printing projects, where they provide reliable threaded interfaces for assembling modular parts without compromising the aesthetics of the finished product. Their adaptability to various materials and industries underscores the importance of selecting high-quality tapping inserts that meet your specific needs.
When evaluating tapping inserts for purchase, consider factors such as installation ease, durability under cyclic loads, and resistance to environmental factors like corrosion. Many online reviews and user testimonials highlight that premium tapping insert kits, though slightly more expensive, offer long-term value due to their reliable performance and minimal maintenance requirements. For instance, tapping inserts designed for plastic applications often include precise tolerances and easy-to-use installation kits that make them ideal for both novice and experienced users.
Industry experts also emphasize the importance of proper training and adherence to installation protocols. Even the best tapping inserts can fail if installed incorrectly, so taking the time to learn the correct procedures can make a significant difference in overall assembly strength. Numerous online tutorials and manufacturer resources are available to help users optimize their tapping insert installation process. By following these guidelines, you can ensure that your assemblies remain secure and efficient over time.
For those in the manufacturing and repair sectors, investing in high-quality tapping inserts can lead to substantial cost savings over the long run. Not only do they prevent the need for complete component replacement, but they also reduce labor costs associated with extensive repairs. Moreover, the ability to quickly replace failed threads with a tapping insert kit means less downtime and a more streamlined production process. As businesses strive for greater efficiency and sustainability, tapping inserts are emerging as a critical component in modern assembly solutions.
Finally, tapping inserts are continuously evolving. With new designs and materials being developed, the market is becoming more competitive, and options are increasing. Innovations such as key locking inserts and press-in variants offer even more ways to tailor thread repair solutions to specific applications. By staying informed about the latest advancements and comparing product specifications, you can choose the tapping inserts that best suit your project needs and ensure long-lasting, reliable connections.
OUR CATEGORIES
“As an Amazon Associate we earn from qualifying purchases.”